Book contents
- Gas Turbines
- Cambridge Aerospace Series
- Gas Turbines
- Copyright page
- Dedication
- Contents
- Preface
- Acknowledgments
- About the Author
- 1 Overview of Gas Turbines for Propulsion and Power Generation
- 2 Review of Thermodynamics, Fluid Mechanics, and Heat Transfer
- 3 1-D Flow and Network Modeling
- 4 Internal Flow around Rotors and Stators
- 5 Labyrinth Seals
- 6 Whole Engine Modeling
- Book part
- Epilogue Current Research Work and Challenges
- Index
- References
4 - Internal Flow around Rotors and Stators
Published online by Cambridge University Press: 25 September 2018
- Gas Turbines
- Cambridge Aerospace Series
- Gas Turbines
- Copyright page
- Dedication
- Contents
- Preface
- Acknowledgments
- About the Author
- 1 Overview of Gas Turbines for Propulsion and Power Generation
- 2 Review of Thermodynamics, Fluid Mechanics, and Heat Transfer
- 3 1-D Flow and Network Modeling
- 4 Internal Flow around Rotors and Stators
- 5 Labyrinth Seals
- 6 Whole Engine Modeling
- Book part
- Epilogue Current Research Work and Challenges
- Index
- References
Summary
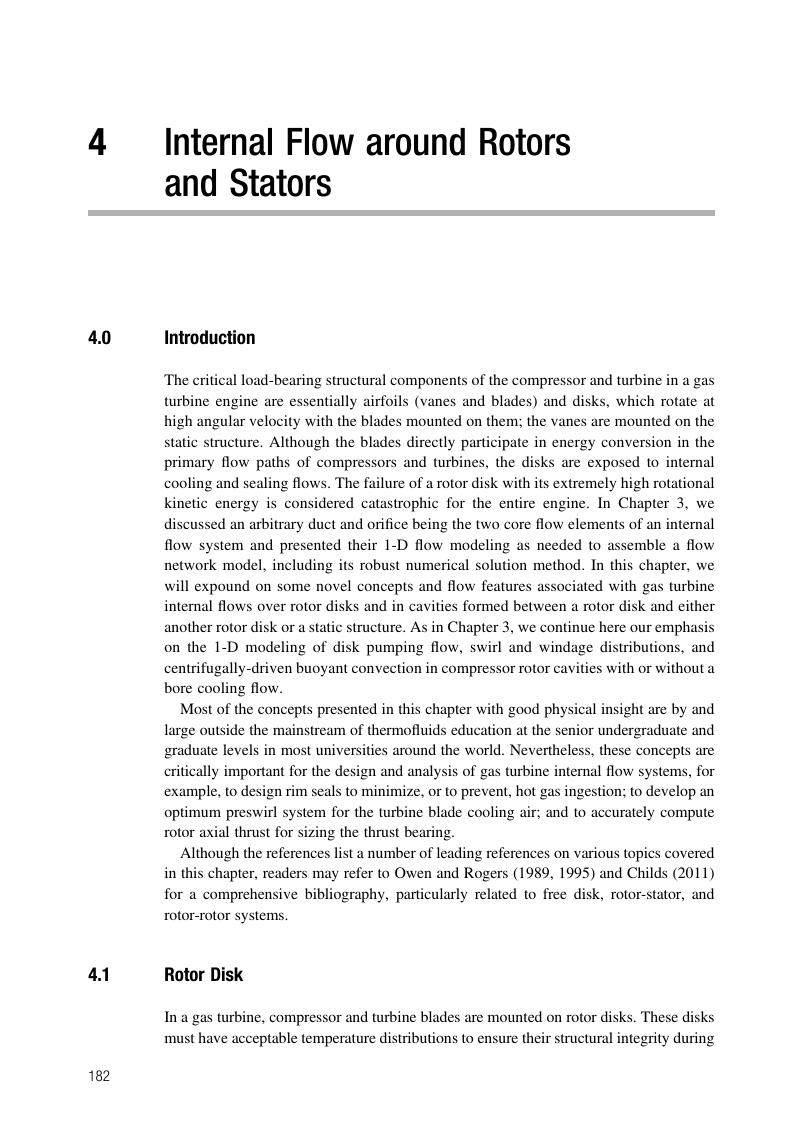
- Type
- Chapter
- Information
- Gas TurbinesInternal Flow Systems Modeling, pp. 182 - 236Publisher: Cambridge University PressPrint publication year: 2018
References
References
Bibliography
- 1
- Cited by