1. Introduction
Organisations collaborate on New Product Development (NPD) programmes to leverage the benefits of expertise across different geographical locations to enable strategy-oriented partnerships, reduce costs and increase quality (Nolan Reference Nolan2012). Collaboration is directly relevant to large-scale, complex, long design and build lifecycle engineering products where there are a wide range of stakeholders contributing to the programme over multiple geographically dispersed locations.
The increasing level of collaboration across multisite-extended enterprises requires appropriate management of product information, which is supported by the concept of Product Lifecycle Management (PLM). PLM is used to assist organisations with the increasing competitiveness in the marketplace across all industries, resulting in a constant need to increase innovation, product time to market, quality, business measurement, protecting intellectual property rights (IPRs) and auditing (CIMdata 2012). CIMdata (2003) described the evolution from Product Data Management (PDM) in the late 1980s and 1990s to the comprehensive PLM used to manage today’s products. PLM was defined as “a strategic business approach that applies a consistent set of business solutions in support of the collaborative creation, management, dissemination and use of product definition information across the extended enterprise from concept to end of life – integrating people, processes, business systems and information.” They went onto state that PDM was first used to manage Computer-Aided Design (CAD) files in home grown systems primarily for engineering, but evolved to PLM and included multiple business functions to increase quality, reduce cost, increase return on investment, improve innovation, increase quality and improve collaboration.
It is useful to distinguish between the different types of product development when considering the implications for PLM implementation. This may be categorised as Make-to-Stock (MTS), Make-to-Order (MTO), Assemble-to-Order (ATO) and Engineering-to-Order (ETO). One differentiator between MTS and MTO relates to the management of the order of an existing design from the customer: for MTS, the order can typically be shipped immediately, whereas manufacturing is required for MTO (Kingsman et al. Reference Kingsman, Hendry, Mercer and de Souza1996). Customisation is possible within ATO in relation to the customer choosing from a range of existing pre-manufactured options (Wikner & Rudberg Reference Wikner and Rudberg2005). Within ETO product development, the customer is responsible for defining the requirements for the product before the design stage, that are subsequently used early within the programme to define the resultant functional requirements of the product (Kingsman et al. Reference Kingsman, Hendry, Mercer and de Souza1996). The development of a First of Class (FoC) naval ship involves both a significant level of bespoke design and engineering, as well as integration of key systems that may themselves require customisation to satisfy the user and functional requirements.
ETO product delivery is complex with many differing elements interacting across the overlapping lifecycle phases, such as concurrent designs of different but integrated systems. This complexity is compounded by levels of uncertainty where design changes have an impact across the programme that are difficult to predict and manage. The complexity is mirrored within the processes and procedures associated with PLM implementation for ETO products – the associated processes need to be at an equivalent level of complexity to effectively support the enterprise system in managing programme complexity. ETO products have a maturing design over many years, and throughout this lifecycle, there will be changes that require configuration, change and quality management processes for example. This is further compounded by manufacturing beginning before the design is fully mature, resulting in product change affecting not just the design, but also potentially causing manufacturing rework. In other product types, manufacturing would not begin until the design is fully mature, with physical prototypes used to test the design and manufacturing and subsequent changes incorporated before full-scale manufacturing commences. A full physical prototype for ETO products would be prohibitively costly and time-consuming due to its scale.
The development of an FoC naval ship that delivers the customer requirements that have been engineered into the solution over the design and build phases is not trivial. Design reviews at designated points within the programme are used to support this delivery. These reviews are event driven, provide confirmation of the completed effort and have representation from the customer, user, contractors and suppliers. The reviews proposed within ISO15288 – system life cycle processes are analogous to those within naval shipbuilding: preliminary concepts review; requirements review; functional baseline review; preliminary design review; detailed design review; pre-test review and pre-release review. The PLM implementation has a requirement to be configured to support each of these reviews.
The approach to requirements management for ETO is another critical mechanism and differentiator for delivery and ultimately provides the demonstration of quality to the customer. Requirements are transformed throughout the programme, starting with the customer requirements defining the need from the operational and in-service support life phases. Functional requirements are defined and agreed with the customer and used to create the functional baseline. These requirements are decomposed into subsystem design requirements and used as a basis to: define the verification, validation and testing of the integrated systems; support traceability between subsystem and system and provide a statement of ‘build to’ for products to achieve function. Requirements management is aligned with the reviews described above, and is facilitated through the PLM implementation.
PLM is required to support the extended enterprise in ETO products. Examples of large-scale, complex, few or one off, long design and build lifecycle engineering products are reflected within the new generation of naval ships for the UK Royal Navy. These high-value ETO products have design and build undertaken across many locations both within the United Kingdom and through a global supply chain (Chan et al. Reference Chan, Huff, Barclay and Copeland1997). Value may be simply regarded as the satisfaction of a need; high-value is defined here as the satisfaction of a critical political, societal and economic need – in this specific case, the means of delivering security of national interests. This research identified that the ETO programme size, complexity, long-lifecycle and lack of the ability to prototype necessitates a tailored approach to PLM implementation. These characteristics of an ETO programme are summarised as follows:
-
(i) Complexity and uncertainty: programme complexity and the associated uncertainty provide significant management challenges within ETO programmes due to the large number of different stakeholders interacting in a large number of different ways to deliver the user requirements through the life of the product (McKendry, Whitfield, & Duffy Reference McKendry, Whitfield and Duffy2015).
-
(ii) Customer commitment: this occurs at an early stage of the programme, with significant input into the design, manufacture and procurement strategies. The customer’s negotiation of requirements, price, delivery dates and product performance should be managed by the prime contractor with respect to quality, schedule and cost with risk management being a key consideration (Rahim & Baksh Reference Rahim and Baksh2003).
-
(iii) Customisation: Hicks and McGovern (Reference Hicks and McGovern2009) posited ETO products as having high levels of customisation typically due to the unique capability required by the customer. ETO products were identified as consisting of an integration of: supplied systems that are bespoke or heavily customised to perform a specific function, as well as commercially available systems that are subject to more general requirements.
-
(iv) Configuration management: the BoM within an ETO programme may be dynamic and influenced, for example, by evolving supplier information which impacts the design. Schedule demands that manufacturing will commence before the BoM is fully mature. Configuration management is used to assess and control BoM changes that can impact the schedule and costs due to rework if not managed effectively (Lee, Kim, & Lee Reference Lee, Kim and Lee2012).
-
(v) Project management capability: project management methodologies require the integration of risk, schedule, resource and governance management supported by a comprehensive set of process models as defined within ISO15288 (Floricel & Miller Reference Floricel and Miller2001).
-
(vi) No physical prototype: prototyping provides a means of assessing opportunities to remove errors and improve efficiency within all life phases leading up to operation of the product. For ETO product development, there is a critical motivation of ‘right first time’ due to the lack of a physical prototype – the FoC naval ship is both the prototype and the delivered product.
Donoghue, Hannola, and Papinniemi (Reference Donoghue, Hannola and Papinniemi2018) conducted a literature review on existing PLM frameworks and stated that PLM initiatives range from Information System change to strategic business transformation. It was concluded that a limitation in knowledge of the business processes may result in failure of a strategy-driven PLM transformation. Therefore, to ensure that a PLM implementation on ETO products is successful requires an understanding of its unique process challenges, which is the context of the business. There is a gap in knowledge with the implementation of PLM on ETO products, which means that the available guidance is insufficient in addressing the objectives of an organisation for NPD in an extended enterprise (McKendry et al. Reference McKendry, Whitfield and Duffy2022). This gap in PLM implementation within the ETO sector is described here with respect to the process considerations. The key objectives for the implementation of PLM on ETO products, the challenges and the enablers required to overcome the challenges and meet the objectives are described from a process perspective. The complete framework has structured these objectives, challenges and enablers in relation to information, process, people and technology.
What is meant by a successful PLM implementation is important to consider. PLM may be considered from a technological perspective as a set of interconnected systems that deliver information-management functionality to support programme delivery (Rangan et al. Reference Rangan, Rohde, Peak, Chadha and Bliznakov2005). There is clearly a need to define the information requirements of the ETO programme through each of the design and manufacturing stages, and ensure the PLM technology is configured to support this. PLM may also be considered from a process perspective – the practices that need to be in place to ensure that the programme is managed efficiently and effectively (Matsokis & Kiritsis Reference Matsokis and Kiritsis2010). For a PLM implementation to be successful, there needs to be designed-in congruency between the PLM information, technology and processes (Hewett Reference Hewett2010). The final factor for success relates to PLM stakeholders in ensuring an appropriately flexible PLM culture is in place to maximise the functional benefit (Fichman & Nambisan Reference Fichman and Nambisan2010). From an ETO programme context, the success of these four perspectives is driven by the motivation of the programme for right first-time delivery of quality, schedule and cost. The process-oriented considerations reported here reflect one of these four perspectives that were holistically investigated, with the informational considerations for PLM implementation within ETO programmes reported by McKendry et al. (Reference McKendry, Whitfield and Duffy2022). There are, however, extensions to this delivery-oriented success for PLM implementation, which are described further within the discussion section. The research aim was to develop a framework to ensure that objectives are met in relation to PLM implementation on ETO products considering the challenges faced due to its unique nature.
2. Process considerations for PLM implementation within ETO
The PLM system is a series of interconnected applications, or system of systems, which perform various functions throughout the lifecycle of the product across the extended enterprise (Terzi et al. Reference Terzi, Bouras, Dutta, Garetti and Kiritsis2010). From an application perspective, the PLM system of systems can be considered to comprise of elements that support: product portfolio management; computer-aided engineering; PDM; customer relationship management; computer-aided manufacture; requirements management; CAD; service management; enterprise resource planning; design collaboration; project management and planning; process management and configuration and change management. Each of these systems provides support in the form of an established digital thread for different and overlapping phases of the lifecycle. In the context of ETO product development, it is important to recognise the almost complete digitalisation of the design process, from concept, system and detail design, as a key differentiator with other types of product development. The use of the digital tools listed above has been established for a number of decades, involves strategic-level decision-making in relation to their choice and commitment over the duration of a programme, is influenced by the controlled environment in which the programme is managed, has practices that have evolved alongside the applications to leverage the benefit and differs quite significantly from the digitalisation of what may otherwise conventionally be described as NPD (Marion & Fixson Reference Marion and Fixson2021). These interconnected systems have their own integration challenges, resulting in numerous examples in industry where the Commercial-off-the-Shelf products are often highly customised by the organisation to meet their capability needs. This system of systems can be integrated for data integration and exchange, and for reporting purposes through a backbone such as a data warehouse where the information is structured and represented based on the source PLM systems (Stark Reference Stark2015). These PLM toolsets are designed to support specific systems engineering lifecycle processes (as defined, e.g., within ISO15288), and typically evolve to improve their functionality to meet these objectives. This has resulted in disparate technologies that were not specifically developed to be integrated in the manner that directly satisfies the organisation’s objectives.
An important requirement of the PLM system is to support processes to capture information and to provide traceability throughout the lifecycle of the product (Matsokis & Kiritsis Reference Matsokis and Kiritsis2010) including providing version and audit management of the product information (Tang & Qian Reference Tang and Qian2008). Procedures to capture this information across the lifecycle of the product in the PLM systems will support design reuse through managing the configuration of the design and its intent (Brunsmann & Wilkes Reference Brunsmann and Wilkes2009). This reuse is supported through the relationships with supporting documentation and workflows, ensuring that when engineers change roles, retire or leave the organisation, the legacy of their work remains within the organisation to be utilised in the future (Brunsmann & Wilkes Reference Brunsmann and Wilkes2009). These structures are necessary not only to ensure that the configuration is maintained throughout the lifecycle of the product, but also to ensure that the design is reusable as is it will provide relevance and ease of access for future interrogation (Baxter et al. Reference Baxter, Gao, Case, Harding, Young, Cochrane and Dani2007).
The information captured in PLM systems across the extended enterprise must be able to be retrieved and understood, resulting in a need to ensure that the processes associated with capturing, searching and displaying the information are robust and efficient to support the knowledge generation activity (Brunsmann & Wilkes Reference Brunsmann and Wilkes2009). The technology must support organisational knowledge management and learning through the integration of project, process and product knowledge (Ebert & de Man Reference Ebert and de Man2008). Organisations are required to support their products through its entire lifecycle, which in the case of large-scale, complex and long-life products can be in excess of 30 years (Conway et al. Reference Conway, Wodehouse, Ion and Lynn2008). The core of the PLM system is typically the Product Breakdown Structure (PBS; Gomez et al. Reference Gomez, Baxter, Roy and Kalta2008) that supports the management and control of the product through object relationships (Schuh et al. Reference Schuh, Rozenfeld, Assmus and Zancul2008) and its associated metadata. The PBS is used to define, capture, manage and configure the BoM and its relationship to supporting information (Schuh et al. Reference Schuh, Rozenfeld, Assmus and Zancul2008). The BoM reflects the way complex products manage and evolve their product information through life (Lee, Kim, & Lee Reference Lee, Kim and Lee2012). Different PBSs are necessary for the various disciplines in complex products and can be represented and integrated to support an Enterprise BoM (Lee, Kim, & Lee Reference Lee, Kim and Lee2012). An Enterprise BoM is used to support the processes of multiple stakeholders who require different levels of information at different phases in the product’s lifecycle.
The Enterprise BoM supports the information needs of multiple stakeholders through the integration of multiple BoM structures, required to support the business processes throughout the lifecycle of the product. The Enterprise BoM should be considered as the master BoM across all the enterprises’ systems (Lee, Kim, & Lee Reference Lee, Kim and Lee2012) in order to avoid any disparate sources that may contain out of date or inaccurate information. The various needs of the stakeholders across the lifecycle of the project should ideally be met by an integrated product development environment (IPDE; Fireman et al. Reference Fireman, Nutting, Rivers, Carlile and King1998) with the PLM technology at its core (Oh et al. Reference Oh, Jeong, Kim, Shin, Yeo and Ryu2008). The aim of an IPDE is to provide the information to support the product development processes in an integrated environment. The management of these processes is not only to support the activities in the product’s lifecycle, but also to ensure that the information can be reused for future opportunities and for legal and contractual obligations (Wilkes et al. Reference Wilkes, Brunsmann, Heutelbeck, Hundsdörfer, Hemmje and Heidbrink2011).
When implementing PLM, the organisation should first understand its strategic objectives and core processes and use this to decide on the PLM approach that should in turn influence the PLM system implementation. This is not trivial as the alignment of business objectives, process and functionality is one of the key challenges to PLM implementation (Bokinge & Malmqvist Reference Bokinge and Malmqvist2012) and is an area that the PLM system vendors have difficulty in resolving (Schuh et al. Reference Schuh, Rozenfeld, Assmus and Zancul2008). This may be due to a lack of understanding on the part of the PLM system vendors about their customers’ needs, which may in turn be due to a customer’s inability to understand their own relationship between strategic objectives, process and technology requirements. Further research is required with respect to the implementation of the technology to align with the organisation’s processes and the strategic vision, with problems arising from tracking performance and quality across the extended enterprise (Nolan Reference Nolan2012).
Whilst there are many technical challenges associated with PLM implementation, the focus of this research is from an engineering management or business perspective. When implementing PLM, it is necessary to be aware of both the technical and business challenges when proposing solutions – this engineering management context is, however, relatively under-researched, particularly with respect to ETO programmes (McKendry et al. Reference McKendry, Whitfield and Duffy2022). The business implications have been recognised; for example, Stark (Reference Stark2011) stated: “PLM is the activity of managing a company’s products all the way across their lifecycles in the most efficient way. In doing so, it enables the company to take control of its products.” Garetti et al. (Reference Garetti, Terzi, Bertacci and Brianza2005) went further to state that the organisational part of PLM implementation may well be harder than the technical part, describing it as a high-intensity organisational activity, and again highlighting the importance of conducting PLM implementation research through an engineering management lens.
Vezzetti, Violante, and Marcolin (Reference Vezzetti, Violante and Marcolin2014) undertook a review of PLM frameworks to investigate the measurement of PLM business readiness with the aim of contributing to the development of a PLM maturity model. They established that the necessary guidance to support the specific business need to assess readiness was not encapsulated in a single framework. Taking a customer-oriented view of PLM, Kärkkäinen, Pels, and Silventoinen (Reference Kärkkäinen, Pels and Silventoinen2012) defined PLM maturity as: “The ability to manage the knowledge and capabilities of an organisation to respond effectively to specific customer needs, at any point in time.” Knowledge and its management are key elements to the definition, with the acknowledgement for proper processes to be created and specified for its management. Key points in time within the context of the development of an ETO product relate to the event-driven reviews discussed earlier, which were not mentioned by Kӓrkkӓinen et al. suggesting that the customer focus of their research was not the application within a Systems Engineering context.
Donoghue et al. (Reference Donoghue, Hannola and Papinniemi2018) investigated PLM implementation frameworks and concluded that whilst useful, they only provided the start of the PLM transformation journey. Using simplified processes, and having a PDM centric PLM environment, gives examples of high-level guidance that is applicable to any business (Sääksvuori & Immonen Reference Sääksvuori and Immonen2008; Stark Reference Stark2015). The PLM framework that Donoghue et al. developed was considered to require expansion to include business strategy, objectives, operating model and products, but was not developed within the context of providing ETO-specific guidance.
Batenburg, Helms, and Versendaal (Reference Batenburg, Helms and Versendaal2006) investigated 23 Dutch organisations and analysed the results to develop guidance for PLM implementation. The extent of the implementation challenge was identified as spanning both the product lifecycle and the extended enterprise, requiring significant changes to be made to the business. They proposed a basis for evaluating PLM maturity in organisations that, on application, established low levels of maturity in these organisations, in particular with reference to organisational policy and strategy. Schuh et al. (Reference Schuh, Rozenfeld, Assmus and Zancul2008) developed a process-orientated PLM implementation framework, focusing on the extent to which PLM functionality was utilised within European SMEs from an ATO, MTS, or MTO perspective. The analysis highlighted a maximum average requirement fulfilment of only 59% for systems integration across these SMEs. The proposed PLM framework linked the PLM software, a PLM knowledge base and a set of reference models.
Bokinge and Malmqvist (Reference Bokinge and Malmqvist2012) reviewed the relevance and the use in the industry of PLM implementation guidance, highlighting the need for organisational improvements relating to aligning organisational processes with system capabilities. They identified a sparsity of research on operational-level PLM implementation, and recognised a need for more thorough studies of industrial PLM implementations to explicitly characterise the challenges that in many studies is implicit. The paper supported the lack of PLM implementation guidelines in general and the need for further research in this respect.
Whilst it is evident that published research in relation to PLM implementation guidance is available, it is apparent that the following limitations exist: failure to take a holistic approach; a lack of understanding of what PLM means; lack of alignment with organisational processes and strategic vision and lack of alignment of organisational processes with system capabilities. McKendry et al. (Reference McKendry, Whitfield and Duffy2022) have developed a synthesis of PLM implementation literature to identify existing gaps.
3. Data gathering and analysis approach
Due to the extent of the influence of PLM within an ETO programme, to develop a framework for PLM implementation on ETO products requires knowledge that comes from a wide range of sources. It has already been established that no detailed guidance or complete frameworks exists on PLM implementation for ETO products (McKendry et al. Reference McKendry, Whitfield and Duffy2022). There are a range of ETO programmes that have recently completed their design and build, with several at various stages of their lifecycle, all of which will have utilised, or are currently applying PLM to some extent.
Merriam and Tisdell (Reference Merriam and Tisdell2015) stated: “In most forms of qualitative research, some and occasionally all of the data are collected through interviews.” They added that “The most common form of interview is the person-to-person encounter, in which one person elicits information from another.” The primary data were collected using semi-structured interviews. Semi-structured interviews reduce the likelihood of observer bias due to the questions being the same for all interviewees. The interviewer has the flexibility to follow up the answers – having the benefit of following a defined pattern but not being constrained by it. This technique also had the flexibility to enable responses that were otherwise supporting or not obvious to flow to the surface, particularly if an answer from one question related to another question (Saunders, Lewis, & Thornhill Reference Saunders, Lewis and Thornhill2009).
The interview schedule was based on the characteristics of ETO products relating to PLM implementation as discussed earlier in Section 2. The questions were designed to capture findings for PLM objectives, challenges and enablers, ultimately to capture the framework for PLM implementation in ETO products. They were designed to have the flexibility to allow the interviewees to expand their responses, and were structured to allow for a comparable set of responses that could be subsequently analysed. The interviews were conducted face to face where possible or via telephone conference where there were significant geographical restrictions. Face-to-face interviews were preferred due to the interviewer being able to follow up on questions based on the facial expressions and body language of the interviewee, and were typically scheduled for 90 minutes. The choice of investigative technique was to record each semi-structured interview and capture the key points in an interview response document (Kothari Reference Kothari2004). The interview questions were initially piloted and then refined, before arriving at the questions and their rationale listed in Table 1.
Table 1. PLM implementation questions
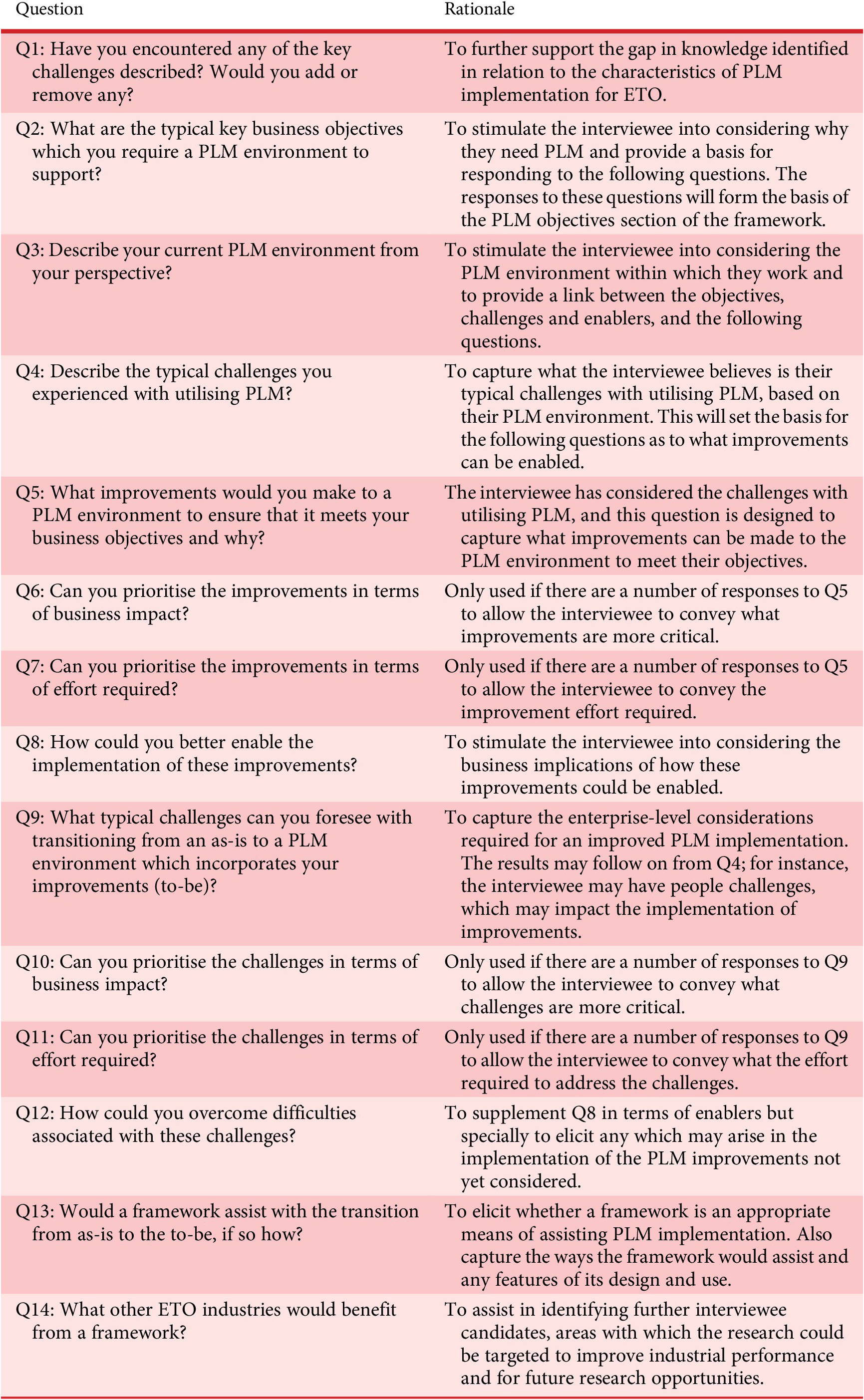
One of the outcomes of the pilot that was identified was a need to provide a more structured and consistent introduction to the research for future interviews. A presentation was subsequently created that provided an overview of the research, its purposes and how the interview responses could contribute to the outcome. Specific aspects that were covered within the presentation included, defining PLM and ETO to ensure that there was a consistent datum, and highlighting the characteristics of ETO programmes as described in Section 1. These characteristics and the above questions had been informed using a combination of published research, and a practical understanding of ETO programmes gained from over 20 years of experience within this industry.
Eleven ETO products were identified from which PLM experts could be interviewed to elicit knowledge to support the development of the PLM implementation framework for ETO products. At least one expert from each of these ETO products was approached for the interview process. The interviewees were selected based on their relationship with PLM in ETO products either as an implementer (responsible for the delivery of PLM capability) or as a key stakeholder (responsible for strategic programme management that is strongly influenced by PLM capability) in its successful use within their organisation. The interviewees were identified through the researcher’s contacts within the ETO industry and through contacting suitable candidates based on research findings, such as from other industries suggested in Q14 of the interview questions.
The next step was to ensure that each of the business functions was represented, including engineering, supply chain, programme management, in-service support, manufacturing planning, manufacturing and IM&T. The customer and the suppliers were also approached for inclusion. Preliminary engagement was undertaken through email to engage potential experts, and through this process, 27 experts were identified and semi-structured interviews on PLM implementation were undertaken from these ETO products in the United Kingdom, France, Australia, the United States and Canada. These experts were: Chief Engineer (A-1); CAD/PLM Design Authority (A-2); Engineering Director (A-3); Project Manager (A-4); Project Delivery Director (A-5); Head of Engineering Strategy and Capability Sustainment (A-6); Head of Detail Design (A-7); Principal Consultant (A-8); Head of Central Engineering (A-9); Quality and Project Management Support Engineering (A-10); Chief Engineer (A-11); Head of Operation and Future Build (A-12); Chief Engineer (A-13); Technical Authority Detail Design and Draughting (A-14); IM&T Director (A-15); Head of Programme (A-16); Supply Chain Director (A-17); Combat System Technical Authority (A-18); Head of Enterprise Systems IM&T (A-19); Nuclear (A-20); Head of Surface Ship Division (A-21); Head of Systems Engineering (A-22); Business Systems Manager (A-23); Wholeship Design Owner (A-24); Head of Platform Engineering (A-25); Lead Combat Systems Integrator (A-26) and Senior Systems Engineer (A-27).
The results of the interviews were captured and analysed to provide PLM implementation recommendations using the NVivo qualitative data analysis tool. The responses were classified into categories (codes and themes), providing a structure for further analysis to take place (Saunders et al. Reference Saunders, Lewis and Thornhill2009). The initial analysis carried out from the interviews was to capture commonality through a coding structure that was then grouped into themes. These themes were used to generate the findings that allowed the analysis and recommendations to be drawn. The phases of thematic analysis used are shown in Table 2.
Table 2. Phases of thematic analysis (Braun & Clarke Reference Braun and Clarke2006)

A nodal hierarchy for the interview questions was initially created in NVivo, and the responses to each question for each interview was then analysed in NVivo. Each interview response to a specific question was given a code in NVivo, which summarised the key point the interviewee was making. These codes were created the first time this key point was made for that question. Further similar key points made by the same or another interviewee had the existing code applied, for the same question. Using the same code for each question allowed the context for the code to be clear within the NVivo nodal hierarchy when further analysis took place. For example, a code which applied to a question on objectives would not be misrepresented as a response relating to challenges. Similar codes could be applied, but they would always be within the context of the question. Once all the interview responses for all the questions had been analysed and coded, related codes were grouped together and a theme was generated. Each theme provided a summary of the topics being discussed that were represented by the codes. The approach to generating the themes is illustrated in Figure 1. An example of the interview responses relating to the process enabler of “PLM business process ownership, development, standardisation…” include: “Standard process, systems and tools will drive consistently with the way people behave”; “Standardisation of approach-you should originally set up to support this 15-year design and build approaches means a programme can be a business within business”; “We cannot allow onerous processes”; “include all the functions and have everyone working towards the same process”; “PLM is a process, it does not matter what toolset you use” and, “It’s a challenge to standardise our business processes.”

Figure 1. Structure created in NVivo to derive the research findings.
Braun and Clarke (Reference Braun and Clarke2006) stated: “Thematic analysis provides a flexible and useful research tool, which can potentially provide a rich and detailed, yet complex, account of data,” but also highlighted potential hazards that may impact the quality of the research. It was important to ensure that the data were collected and analysed across the entire content of the research – in this case, all of the interview responses, from all the interviewees. In this respect, the research mirrored the approach described by Robinson starting with a priori theme selection (Robinson Reference Robinson2021). These a priori themes were influenced by Enterprise Architecture that is used to describe the business strategy, model, objectives, processes and technology of an organisation. One consideration within the use of Enterprise Architecture is in defining the ‘ai-is’ problematic aspect of the business, which can in turn be used to plan the ‘to-be’ target environment (Foorthuis et al. Reference Foorthuis, Hofman, Brinkkemper and Bos2009). The business architecture provided a focus on people and process in order to meet the needs for the management of delivery. The process theme formed the basis for the research published here. The analysis was also categorised in relation to moving from an ‘as-is’ problematic, to a ‘to-be’ target by further considering objectives, challenges and enablers for process PLM implementation considerations. The themes should be supported by the data themselves to ensure that they are not generated based on weak data; therefore, there should be data to support each of the themes (Braun & Clarke Reference Braun and Clarke2006).
4. PLM implementation framework – process implications
This section describes the findings from the thematic analysis of the responses from the semi-structured interviews including the main themes derived from the interview responses that are used to develop the process implications of the PLM implementation framework. The interview responses also highlighted commonality in relation to how the interviewees responded to the PLM implementation questions. Relevant literature was also used to provide evidence or otherwise of the dependability of the themes, and is included in the descriptions. A summary of the supporting interview statements for the framework’s process objectives, challenges and enablers is provided in Sections 4.1–4.3, along with recommendations in relation to implementation. These sections do not include all interview responses used to derive the themes or a complete narrative of the analysis, instead focusing on concisely summarising the key points in order to get a broader illustration of process objectives, challenges and enablers.
4.1. Process objectives
Effective PLM business processes are important for any NPD, and those objectives identified in this section are supported from literature related to ETO or other similar product types. ETO products differ due to the increased levels of complexity and uncertainty throughout the development phases of the lifecycle that requires adaptation of the PLM business processes. This section describes those PLM implementation process objectives for ETO products that were identified from the interview responses through the thematic analysis, and is synthesised with relevant literature. The concepts that are used to describe the process objectives within this section are illustrated in Figure 2, summarising the relationships between the PLM process objectives. Processes to support product development and build collaboration across all stakeholders in ETO products are important, as is ensuring that the schedule and cost is managed to maximise profit, to reduce risk and provide value for money for the customer. As ETO products are highly customised, identifying and enabling standardisation in design and build is another objective discussed in this section.

Figure 2. Product lifecycle management implementation process objectives.
4.1.1. Support the design and build for product safety and environmental considerations
The design, build and in-service support of an ETO product must use processes to ensure that safety, health and environmental (SHE) obligations are correctly managed. PLM may be used to support this objective through providing processes that enable the necessary SHE information to be captured and managed throughout the product’s lifecycle. Stark (Reference Stark2015) stated that PLM can provide assistance in capturing and formatting information to meet SHE regulations, as well as providing audit trails of decision-making traceability. Duque et al. and Barreto et al. discussed how PLM may be used to support green manufacturing and sustainability by tracking materials used in the product throughout its lifecycle. This was supported through the interviews such as with A-1 who stated that PLM provides evidence with regard to the management of information to support product safety. Providing evidence of design for product safety is an important element of all NPD, is particularly challenging within ETO and PLM should provide this evidence when required. Investigations of previous product failures such as with the Nimrod crash, identified a lack of evidence of design for product safety and included in recommendations for improvement (Haddon-Cave Reference Haddon-Cave2009).
The challenges specific to ETO products require robust PLM processes relating to SHE such as ensuring correct data formatting and attribution (McKendry et al. Reference McKendry, Whitfield and Duffy2022). However, as stated by A-24, PLM also allows appropriate engagement from the product safety team to ensure that they can influence the design. This is achieved in a number of ways including access to the emerging product information across the extended enterprise throughout the lifecycle. As the data are structured in a configured way with a full audit history displaying how the data evolved, it makes it considerably easier whilst undertaking the business processes to understand any SHE implications. A-20 also stated that safety considerations are a key business objective for PLM. This enables the NPD stakeholders to support and monitor the evolving product development throughout its long lifecycle, and provide SHE reports directly from the PLM environment. It will also provide evidence to the appropriate regularity bodies that SHE legislation is being met.
4.1.2. Enable quality through right first time and reduction in rework
ETO products typically lack a physical prototype – an FoC naval ship is both a physical prototype and the delivered product (McKendry et al. Reference McKendry, Whitfield and Duffy2022). They have overlapping life phases with design areas reaching maturity at different times with emergent product development behaviours impacting the programme. Hicks and McGovern (Reference Hicks and McGovern2009) stated that “ETO products are subject to product change through the lifecycle of the programme.” These can result in quality issues that can have a significant impact on the programme schedule and cost due to unplanned rework. The cost of quality increases as the programme matures, with resultant cost, schedule and reputational damage.
Quality is a topic that was consistently discussed both in the literature and in the interview responses. The literature in Section 2 highlighted the role that PLM has in improving quality and reducing rework throughout the lifecycle of the product. A-2 and A-25 raised a key objective for PLM to support the reduction in rework due to improving quality, therefore reducing cost to the programme. A-12 provided the example of ‘lifed’ items, described as those components that have a specific life, when they are required to be replaced. The information and related processes must be managed effectively, including item description, location, fitting date and maximum life span before replacement.
In ETO products, these components number in the many thousands and a poor PLM implementation in this respect will result in considerable cost in the manufacturing phase as the programme stakeholders attempt to understand what items need replacing and when. A-10 and A-20 both stated that in hazardous ETO environments such as a nuclear facility or a particle collider, the quality considerations are critical as rework has a considerable cost: once an item has been fitted in a radiated environment, for example, it cannot be easily removed. PLM supports improving quality and reducing rework by managing the evolving design, build and maintaining the product in-service, and assists with the management of emergent product development behaviours throughout the product’s lifecycle. This includes identifying the implications of these behaviours to ensure that quality is not impacted and rework is reduced.
4.1.3. Enable product development and build collaboration across all stakeholders
PLM is required to assist with the mobilisation, integration and collaboration of stakeholders throughout the lifecycle of the ETO product. Due to the scale and long lifecycle of the ETO product, there are thousands involved who have various skills and functional objectives. They will be in different geographical locations and from different organisations. As discussed earlier, enabling collaboration throughout the NPD process is a widely considered and fundamental objective of PLM in the literature. Gomez et al. highlighted how PLM removes traditional problems of silos of information and will enhance collaboration across the extended enterprise (Gomez et al. Reference Gomez, Baxter, Roy and Kalta2008). The ability to mobilise disparate and physically dispersed stakeholders towards collaborating on a design was also captured throughout the interviews by A-14 and A-17. Examples include the integration of engineering processes with those of manufacturing planning to ensure that the design can be effectively built, supporting a shared situational awareness. This also allows manufacturing planning to have visibility of the design to allow them to undertake their planning processes earlier, therefore reducing the lifecycle of the programme and consequently reducing risk. The same can be said for other business processes such as collaboration with engineering, product safety and the commissioning of the build as raised by A-2. The interviewees did not widely raise collaboration as an objective of PLM considering its importance and relevance. This may be due to collaboration using PLM being a fundamentally accepted requirement for their organisations, similar to security, export and IPR requirements.
The PLM processes deployed must ensure that each stakeholder understands how to achieve their deliverables including the interfaces with the processes used by other business functions. These processes may be used by thousands of stakeholders across multiple geographical locations. ETO products will rely on PLM to support understanding of the emergent process behaviours such as product change, and its impact on the various business function processes.
4.1.4. Cost, profit, risk reduction and value for money
An objective of PLM is to assist in the management of risk through processes that enable the capturing and presentation of the programme information. This supports the management team in identifying and reacting to programme performance. The need for cost management as an objective for PLM was also captured within the interview responses. A-22 stated that PLM must support profit for the business providing more for less, and supported by appropriate metrics. A-5 stated that information is the building block to drive and sell your product, and that if you can control your information, you can better control cost and therefore your price. Without PLM within ETO programmes, the effective management of programme cost and schedule would be compromised.
The importance of profitability to an organisation was raised by A-26 as a key objective of PLM. This is due to the ability of PLM to reduce rework and as a risk reduction for exposure to warranty costs. A-26 stated that PLM is a key resource for customer satisfaction through providing value for money and improved assurance that the product meets the customers’ requirements. PLM helps in supporting understanding of customer risks; therefore, they can be managed more effectively that will drive risk reduction, as was identified by A-24. Therefore, PLM will also assist in managing the programme performance and provide assurances to the customer that they are receiving value for money by proving appropriate metrics on programme performance, such as with the design maturity against the plan or the status of identified risks.
4.1.5. Enable standardised design and build
As described in Sections 1 and 2, the literature on PLM for ETO products is relatively sparse. The objective of providing standard design and manufacturing processes to the design and build of large-scale, complex products given their unique challenges is not widely discussed. Pulkkinen, Leino, and Papinniemi (Reference Pulkkinen, Leino and Papinniemi2017) discussed how PLM could enable the standardisation of manufacturing processes, but also commented that further research was required in order to achieve this. PLM enables standardisation of processes such as with the Siemens Process Framework (Rohloff Reference Rohloff2009), but these do not provide guidance on the challenges of ETO products and the difficulties with standardisation. These challenges include the high levels of customisation characterised within ETO products as discussed earlier, which results in difficulties with standardising design and manufacturing processes.
The lack of a physical prototype also means that design and manufacturing processes cannot be refined using prototypes. Due to the highly customised nature of ETO products and the lack of a prototype, there are a significant number of processes that are non-standard and therefore not repeatable, particularly in the build phase. This leads to inefficiencies and risks to quality and safety due to the limited opportunity for continuous process improvement.
One interviewee stated that a key objective of PLM was to enable standardisation in the design and build. A-12 stated that there was a need to introduce standardisation as the whole product could not be prototyped; instead prototyping aspects of the product, examples include identifying repeatable manufacturing processes in build and relating back to the design process. Therefore, an objective of PLM is to assist in the identification and management of processes that can be standardised, with the resultant opportunities for continuous improvement. These improvements can be used to influence other stakeholder processes, such as improving design for build or support.
4.2. Process challenges
This section describes the challenge of creating processes that meet business objectives and are not overly complicated. This challenge was synthesised from the interview responses through thematic analysis and was the only process related challenge that was identified from the thematic analysis for the implementation of PLM in ETO products. The analysis of the interviews identified that creating processes to meet business objectives was required, but that it is difficult to align this with processes that are manageable, flexible and easy to understand due to the level of complexity and uncertainty in ETO products. The examples described within this section are illustrated in Figure 3 that summarises the relationships between the challenges for PLM processes.

Figure 3. Product lifecycle management implementation process challenges.
4.2.1. Creating processes that meet business objectives and are not overly complicated
There were numerous examples from the interview analysis where PLM processes were developed and implemented to meet ETO business objectives that have been over engineered. A-2 stated how they incorrectly made their electronic process workflows in the PDM system overly complicated and prescriptive, resulting in difficulties when something went wrong and needed to be fixed. The result was that they had to reengineer their workflows to make them simpler. The creation of complicated processes, including those that are replicated in the PDM workflows, is understandable given the complexity of ETO products, but flexibility is required to manage emergent product process behaviours such as change. Moreover, an objective of PLM in ETO products is to manage security, IPR and export obligations as discussed in earlier, and these require PLM processes with multiple stakeholders and strict rules, which if breached can have significant consequences.
A-1 highlighted the difficulties associated with identifying IPR information that cannot be shared across different ETO programmes, and used the example of a diesel generator that might have information embedded in the detail that cannot be shared. A consequential failure to implement processes to manage obligations may result in a breach of security, IPR or export controls.
Another example of the challenges of managing process complexity is with non-recurring activities. ATO products typically have repeatable processes that can be refined and improved upon, with associated learning gained from each application. A-16 highlighted the difficulties associated with planning of non-recurring tasks that are typified within the novel nature of ETO products, where the processes may be defined and used for the first time. The difficulties associated with creating a programme plan were highlighted, if processes are at a high-level, and cited the example of managing product reviews.
The challenge is therefore to achieve an appropriate balance between overly complicated processes that lack flexibility, and processes that are too simple lacking the detail required to support the business objectives. Processes should also not be constrictive due to the level of uncertainty in ETO products. A-17 discussed the challenges related to the focus on schedule adherence when implementing improvements on the programme, one of which related to insufficient attention being paid to realising strategic objectives. This balance between having the right level of process detail to manage uncertainty in the programme, having processes that can be applied to accomplish programme objectives and to measure cost and schedule adherence, as well as the overall programme performance, is a challenge that needs to be addressed.
A-12 discussed how their business is building a bespoke product that is tailored to meet unique customer requirements, that consequently necessitated the development of tailored business processes. A-12 introduced new processes to identify products that can be manufactured repeatedly. This was a new approach with a greater level of flexibility, required in order to adapt their business processes as they learn through the ETO programme lifecycle. Ensuring that these processes are not overly complicated is difficult when they have never been applied before. Another difficulty in ensuring that processes meet the business objectives is guaranteeing that all the stakeholders in the ETO programme are using the same approach. Differing, non-standard processes can result in a significant impact to ETO product delivery due to a misalignment on objectives. A-26 cited an example where partners in his programme have different specifications for testing, resulting in constant rewrites of the test specifications to meet business objectives.
It is also important to adhere to processes that have been agreed. A-2 described that a challenge for the successful use of PLM is with process documentation, as people often work around processes, tailoring them to satisfy their need, and therefore problems or improvements are not captured as these workarounds are local and not documented. A-10 also stated that there needs to be more focus on process adherence to support the PLM deployment. A-27 described that a challenge with standardising processes is that they have a business model that was developed before their PLM implementation and the associated technology. A-27 added that it is a challenge to standardise their business processes, not least because there are many different opinions across multiples programmes that go through different lifecycles. It was then stated that understanding what those processes are and what data are required to be managed is difficult, particularly for those who are new to PLM. Therefore, there is a challenge with integrating and standardising processes to meet the objectives of different programmes.
Overly complicated processes will not only inhibit the ETO product design and build, but will also lead to failures in meeting mandatory regulations such as safety, health, environment, security, IPRs or export controls as onerous processes are bypassed. Where processes are bypassed, workarounds are not documented and potential improvements are lost with problems not communicated to the responsible stakeholders. Due to the customised nature of ETO products and the lack of a prototype, processes may require to be created as the business objective or challenge emerges. This results in a novel approach that may have been used for the first time. Therefore, there are difficulties in ensuring that a process is fit for purpose before deployment, such as managing security, maturity, design reviews or with business improvement initiatives in design or build. Other product types, such as automotive manufacturing, have repeatable processes that are proved and enhanced through testing on prototypes, and continuous improvement techniques such as Lean. There is also the challenge of ensuring that processes do not strip out necessary detail, and are therefore not fit for purpose, in an attempt to ensure that they are not overly complicated. Processes should manage the uncertainty in the programme, but also support the schedule and cost to ensure overall programme performance.
4.3. Process enablers
This section describes those process enablers for the implementation of PLM on ETO products that have been synthesised from the interview responses through thematic analysis. This enabled subsections to be created that describe the process enablers, which include the ownership of PLM business processes, their development, standardisation, Learning From Experience (LFE) and adherence using suitable expertise within a dedicated cross-functional team. The concepts that are used to describe the process enablers within this section are illustrated in Figure 4, summarising the relationships between the PLM process enablers. Ensuring guidelines and governance over process complexity to ensure they are simple and usable is another enabler as is mandating the utilisation of PLM processes internally, to partners and the supply chain.

Figure 4. Product lifecycle management implementation process enablers.
4.3.1. PLM business process ownership, development, standardisation, LFE and adherence using suitable expertise within a dedicated cross-functional team
The PLM business processes used to support ETO NPD should have appropriate ownership for development and maintenance to support the various business functional activities that they represent. The processes should also be standardised to support the various interconnections of the business functions to ensure that disparate processes that only support individual programmes or activities are not created. A dedicated cross-functional PLM team will enable not only both ownership and development of the processes, but also integration with the other business units. This team will also ensure adherence within their own business functions and target any disparate processes that do not support the PLM objectives of the business. Ensuring that LFE is captured from within the programme, any legacy programmes and across industry and academia will also be enabled by the team.
A-14 stated the importance of ensuring that the PLM strategy is not driven by an individual programme, but spans all programmes within the business. A-14 added that they have used PLM differently across a number of programmes as each is tailored to individual programme needs. They typically start PLM from ‘scratch’ for each programme with the resulting effect of having a slightly different PLM system for each programme. It was then stated that PLM should be owned by the business and not driven by the programme, but with a central function managing PLM. There should be standardised business-wide processes and technology that will drive consistency with the way people behave and will assist in eliminating data quality issues experienced by the programme. A-14 provided examples of how, across programmes, people bring their own ideas, resulting in variations in the processes, technology and in the designs themselves. As a result of these variations, the business does not always get the benefits from translating design content from one programme to another and that, accordingly, people become frustrated. Further examples were provided that illustrated if there is standardisation of PLM across the business, then it would reduce the time to undertake tasks, resulting in improved schedule adherence and making the business more cost effective. A-14 also described how the requirement for training would be reduced if there was standardisation across the business as more process variation usually means more training.
In order to ensure standardisation across the business, a cross-functional PLM process team with the appropriate authority and Suitably Qualified and Experienced Personnel (SQEP) should be created. This will include process development, ownership, ensuring adherence and also providing central communication to the technology providers to ensure that requirements meet whole business objectives and not just those of the individual programme. This will reduce technology variations across the business, resulting in reduced customisation, lower risk to the programme and will enable the IT function to better focus their resources on the key business requirements.
A-13 described how an enhancement to their PLM environment would be to have improved team integration with different functions embedded within teams to advance the way they work together; this would also enable quick access to the right skillsets. The ETO product is complex, so there are skilled resources supporting the various processes across the functions, such as system design engineers, detail design engineers, supply chain professionals, programme managers, finance personnel, manufacturing planner, manufacturing engineers, test and commissioners and in-service support engineers. Having representation from these functions would assist with the success of the PLM approach by ensuring that the processes and enabling PLM technology meet the needs of all functions across the lifecycle of the product.
A central PLM team was also supported by A-9 who stated that to resolve the issues associated with PLM delivery, it would be beneficial to have a centralised team to provide PLM administration, standardisation and ensuring that it is consistently practicable. It was added that they would provide economies of scale where the overall programme would benefit by utilising key resources centrally to leverage their skillsets to meet programme objectives. A-9 also stated that this central team can be used to enable LFE and that, ultimately, centralisation would provide benefits that ensures that the same problems are not repeated, which has been the case on previous programmes. It was cautioned that this may be seen as empire building by some, but that can be mitigated by gaining buy-in from across the organisation, not least by explaining the benefits centralisation will bring.
A-14 stated that they do not have a surplus of resources who have the knowledge and experience in the PLM processes and technology and that it is difficult to recruit SQEP due to the unique nature of their product and its complexity. It was questioned whether external resources would understand the difficulties with their product and whether they would understand the processes. Internal skilled resources, however, have other demands placed on them to meet the challenging programme schedule and that they often rely on resources for the PLM implementation that have other responsibilities. Therefore, there is a lack of dedicated focus on the PLM implementation from these skilled resources. A-14 speculated that their organisation does not do enough to establish the relationship between the issues and the technology requirements, causing difficulties with implementing a solution into the PLM environment that addresses these requirements. The solution is typically implemented whilst undertaking the product development activities. Having a dedicated PLM team would enable the focus to be on the PLM implementation without being distracted by other activities. There would also need to be a balance between replacing these skillsets and building up experience in other team members.
A-10 described the difficulties with using the technology providers to assist as they do not understand the requirements of the ETO product, they have a very IT approach, and they focus on selling their products. A-3 stated that an improvement to their PLM environment that meets their business objectives would be to use PLM earlier in the lifecycle; however, it must be appropriate to the needs of the programme and be scalable to support business processes with the necessary control. The dedicated SQEP PLM team would provide this improvement by introducing repeatable processes and enabling technology proved in previous programmes. This team would have the necessary skills and experience from across the business. A-2 also supported the use of a dedicated PLM team, and stated that their organisation has process owners, but that they also undertake ETO product development activities, so they will not have the capacity to create these processes. A-2 added that they overcame this challenge by creating a central team that creates and maintains these processes, in alignment with the core PLM architecture and principles that can be explained to the business.
4.3.2. Guidelines and governance over process complexity to ensure that they are simple and usable
Ensuring that processes deliver the business objectives whilst not being overly complicated was identified as the only process-oriented challenge. A-9 stated the importance of ensuring simplicity with the processes, for example, ensuring that electronic workflows in the PDM system are not technology-driven with vendors directing the solution. This was added to stating that if a dedicated PLM team is created and there are integrated processes and systems with a master record approach, then this will assist with process simplicity. A-16 cautioned that the business should not be too prescriptive and that flexibility is required to assist with the complexity of the programme. A-7 described how there is a need to ensure that there are no local approaches to using PLM as that may result in quality issues, resulting in a lack of information required to understand the root cause. This point was embellished stating that PLM can be used to mandate how the business operates.
A-14 stated they must not have processes that are too onerous, for example, where electronic workflows are too complicated, adding that they keep the processes simple and endeavour to continue to do so. A-2 also highlighted how they made their electronic workflows in their PDM system too complicated and prescriptive as they believed that everyone would use the same workflow. This led to it becoming too large to support all the process variations, and that if something went wrong in the workflow, it was difficult to fix. A-2 described how they had to completely reengineer the workflows to make them simpler and easier to support, with the key being to keep things simple. As shown earlier, there was evidence to demonstrate that due to the complexity of the ETO product, processes are created that reflect this complexity, and subsequently make them unusable. A balance must be struck between ensuring that the processes are robust and meet the business needs, but that they are also simple, usable and are easy to understand across the large number of personnel in the programme from various functions and backgrounds. This simplicity will also aid in ensuring that those electronic workflows, which are based on the business processes, can be maintained and are flexible to meet the emergent needs of the programme. Therefore, there should be guidelines and governance managed by the central PLM team to ensure that the processes do not become overly complicated when attempting to meet the business objectives.
4.3.3. Mandate utilisation of PLM processes internally, to partners and the supply chain
There is minimum advantage to the ETO NPD if PLM processes are created to support business objectives, but these are not made mandatory for use by all those involved in the extended enterprise. A-21 used a supplier perspective to describe how important it is for suppliers to understand the programme’s maturity management approach and the relationship with the product information they provide. The information provided by suppliers is used to progress the evolution of the design and often this is at various levels of maturity at different life phases in the programme depending on the level of customisation, as discussed in Section 2.
A-21 stated that, as a supplier they want more knowledge of the design systems their product will interface with across the ETO product and how they can help with the integration. This relationship between the supplier information and the maturity management is an important enabler for a successful PLM implementation on ETO products as the suppliers provide technical information used to evolve the product development in the programme. To ensure a successful maturity management approach, key suppliers, especially those for critical design systems, should understand how the information they are providing is being used by the programme to reflect the maturity of the product.
A-26 described how to start from the beginning of the programme and ensure that the contracts have clauses stating that stakeholders and relevant suppliers must adhere to the PLM approach. A-26 added that it should be stipulated that they must use the same integrated environment and that they cannot subsequently create their own technology systems, which is an important point in relation to achieving a single point of truth.
As there are many stakeholders in ETO programmes, having contractual obligations is important to ensure the prevention of disparate, unintegrated systems, with the resultant information quality issues. In conjunction with the contractual obligations, the stakeholders must also be supported by the PLM team who can provide support and help to ensure buy-in of the programme’s PLM approach. The PLM team can also aid in assuring that adherence to the PLM approach is maintained.
As described by A-21, suppliers would be willing to support the PLM approach if they understood it. However, without the contractual obligations, as stated by A-26, there is a risk that when costs and schedule impact the delivery to the programme, the stakeholders may fail to follow the PLM approach. Having an appropriate balance between supplier engagement and overly constraining them by the PLM processes is important. A-17 highlighted the importance of allowing suppliers to innovate to assist with the product development process.
A-20 stated that they would prefer long-term collaboration with suppliers to build relationships and highlighted the difficulties with having to go out to the market for each new programme in order to meet value for money conditions set by the customer. A-20 stated a preference for a healthy supply chain that is not overly reliant on their business. Since ETO products have a long lifecycle, there is a risk that if a supplier is too reliant on a single programme, they may become insolvent within the product development cycle. This would impact the information used to progress the product development as well as the final delivery of the hardware during the manufacturing phase. In addition to engaging with suppliers on their responsibilities within the PLM approach, monitoring the wider health of their business is important. Through this engagement, the skillsets of the supply chain and the wider stakeholders will increase, improving the understanding of PLM in the programme.
5. Framework validation
Evaluation reflects the judgement or determination of the quality, importance, amount, or value of something. Validation provides evidence that something is correct, which, in this context, relates to whether the framework contains the necessary elements for the implementation and successful use of PLM on ETO products. Borrego, Douglas, and Amelink (Reference Borrego, Douglas and Amelink2009) stated in relation to the aim of evaluation in qualitative research: “The goal is to establish that the results provide convincing evidence sufficient to answer the research questions.” The previous section describes the processual elements of the framework for the implementation of PLM on ETO products focusing on objectives, challenges and enablers. This section presents an assessment of the validity of the framework that was undertaken using the following stages:
-
(i) Preliminary evaluation through the presentation of the framework for initial feedback on structure and content. This was to gauge initial reaction to the structure of the framework to ensure that it was easily understandable.
-
(ii) Main evaluation and validation through the presentation of the framework to selected participants followed by a questionnaire. The questionnaire contained statements to evaluate and validate the framework quality, structure and versatility.
-
(iii) The industrial application of the content of the framework in an ETO product. This section describes how elements of the enabling themes identified in the framework were used to develop the PLM approach in BAE Systems Maritime Naval Ships.
Nowell et al. (Reference Nowell, Norris, White and Moules2017) have provided a list of six criteria that may be used to assess the trustworthiness of thematic analysis research: credibility, transferability, dependability, confirmability, audit trails and reflexivity. The credibility of the findings may be tested with member checking using previously interviewed respondents to test the representation of the themes identified (Côté & Turgeon Reference Côté and Turgeon2005). Transferability has been described as the generalisability of the findings across different sites (Nowell et al. Reference Nowell, Norris, White and Moules2017), and was also considered within this research through the selection of participants from industries manufacturing different ETO products. Dependability was considered within this research in relation to seeking the existence of confirmation within published research for the identified themes. Where possible, published literature was used to either confirm or contradict the themes.
5.1. Preliminary assessment of framework structure
Three presentations were delivered to capture initial feedback on the structure of the framework and assess its ease of understanding and coherent layout. Presentation slides were used to describe the research to provide context, followed by an overview of the framework developed from the thematic analysis. The presentation was structured around all four key elements of the framework: people, process, information and technology, using objectives, challenges and the enablers. A first draft of the framework was presented to the participants.
The first presentation took place using two participants with a significant interest in PLM implementation on ETO products from BAE Systems Maritime Naval Ships. These two participants had not previously been interviewed at any stage, but were aware of the research. This approach was chosen to capture feedback from participants who had not been previously involved to gauge the content, structure and ease of understanding of the framework. The feedback was positive and both confirmed that they believed the framework would be of significant benefit to the implementation of PLM on ETO products. They questioned why relationships between each of the themes of the framework had not been developed to more easily understand how an enabler could overcome a specific challenge to meet an objective for example. The researcher described that the framework was developed to be flexible and scalable, and that by adding relationships between the themes may be overly constraining in its implementation. They agreed that this would be necessary due to different programmes having different objectives and challenges. It was also important to enable flexibility due to the emergent challenges in ETO products, for example, there are programmes that require greater focus on processes whilst already having a mature PLM technology architecture.
The second presentation took place with a single participant who again had a significant interest in PLM implementation on ETO products from BAE Systems Maritime Naval Ships, but who had previously been interviewed. This enabled feedback from someone who understood the research aims and objectives and had contributed to the findings. The participant stated that the themes and the framework structure were extremely valuable and would provide significant benefits to PLM implementation on ETO products. It was added that the ‘enablers’ were useful as they would support the development of a new, more skilful, talented and technologically aware generation of engineers in the business. The participant described a desire to take the framework from inventive to exploitation and utilise it in an industrial capacity. It was additionally suggested that the framework and the background detail could be integrated electronically to aid understanding – a theme could be selected and the stakeholder presented with the relevant underlying information.
The final presentation and discussion of the framework took place with a single participant with a significant interest in PLM implementation on ETO products, who had previously been interviewed, but was from an export customer. The feedback elicited was that the findings and the framework would provide significant benefits to their company and that it would steer the direction of their PLM strategy. It was opined that the framework provided a very useful presentation of the summary of the results, and a request was made for a document that described the overall research as this would help communicate this new approach to his business.
5.2. Main framework validation
Following the preliminary assessment, a questionnaire was used as the main approach to capture the opinion of the senior stakeholders in ETO products who have an interest in the successful implementation of PLM. A questionnaire was chosen to focus the participants on the framework quality, structure and versatility and was formed around a series of statements that were developed to elicit a response relating to the extent that the participants agreed. These responses related to the validation objectives for the quality of the PLM framework, indicating the extent that the framework contains the necessary elements for the implementation and successful use of PLM on ETO products. Responses were also elicited in relation to the PLM framework structure and versatility. To enable this, eight statements relating to the evaluation objectives were developed (illustrated in Figure 5).

Figure 5. Proportion of responses to framework statements.
These participants were selected from business functional roles, or partner organisations within the extended enterprise, all within senior positions, and were stakeholders in the successful implementation of PLM in ETO products. The organisations were chosen due to their involvement in various multi-£B ETO programmes, and across different ETO products who may have different customer constraints, for example, government practices. The roles within these ETO organisations were selected to represent stakeholders who have business objectives required to be met by a successful PLM implementation. The participants were a mixture of those interviewed to generate the findings, those aware of the research but not interviewed and those with no knowledge of the research. The participant roles included: Head of Manufacturing Planning (B-1); Engineering Manager – In-Service Support (B-2); Engineering Manager – Design (B-3); Manufacturing Planning Manager (B-4); Engineering Manager – BoM (B-5); Engineering Manager – PLM (B-6); IM&T Manager (B-7); PLM Consultant (B-8); PLM Architect (B-9); Design Authority (B-10); Operations Manager (B-11); Head of Engineering (B-12); Head of Enterprise Architecture (B-13); Head of IM&T (B-14); Underwater Systems Specialist (B-15); Programme Director (B-16); Deputy Head of Programme Management (B-17); Systems Engineering Manager (B-18) and Engineering Director (B-19).
The approach to the main validation was constructed to consist of identifying participants who would attend a 1-hour workshop, either face to face, or via a teleconference with shared media. The participants were engaged in the evaluation either on a one-to-one basis, or in small groups in a 1-hour session with the intention of communicating the research aims and methodology through a presentation describing the PLM implementation framework, followed by a description of the questionnaire structure. The participants were then asked to re-read and complete the questionnaire in their own time (Bell, Bryman, & Harley Reference Bell, Bryman and Harley2018) following the session, allowing time to reflect on the material presented. The participants were requested to rate their level of agreement or disagreement towards the statements using a five-point Likert scale. The range of options were: strongly disagree, disagree, neutral, agree and strongly agree. This approach and the wording of the statements were used in order to not lead the participant to a particular rating. The responses to the questionnaire questions relating to framework quality, structure and versatility are shown in Figure 5, illustrating for each question the proportion of responses for agree/disagree.
The responses to the questionnaire statements supported the objectives of the questionnaire for quality, structure and versatility with 95% of the responses either agreeing or strongly agreeing with the statements. The comments included within the questionnaire responses also supported the value of the framework. B-1, for example, highlighted that in their experience, there is an overreliance on technology to support PLM objectives and that it is the human factor present within a cross-functional team that supports the successful implementation. B-1 added that it is refreshing to see this represented in the framework. B-17 highlighted that “securing the support of the business is, and will always be, a key challenge and a very important enabler.”
The comments also highlighted the importance of versatility, with B-2 stating that tailoring was important whilst acknowledging that the framework described their business challenges. B-11 stated that they were already adapting the framework: “The framework as specified is being tailored for use on a number of new/prospective programmes.” B-11 went on to describe how the framework provided a scalable and tailorable approach for PLM implementation in a complex environment. B-14 commented that they are currently implementing PLM on an ETO programme and that “this framework hit every aspect of the issues in the PLM install programme today.” B-16 stated that the framework “would be useful to our organisation as we begin the implementation process.”
The framework was described by B-3 as being ‘an invaluable asset to any business embarking on the implementation of PLM’. It was also highlighted by B-3 that the wide and varied research approach was a strength, including different ETO products, and included key themes that B-3 identified during their PLM implementation. The systematic way that the framework considered the key elements in PLM implementation was identified by B-6, and was supported by B-9 who described it as robust and well considered and B-17 stated that the framework “was well thought out.”
B-10 highlighted that the framework structure is a ‘noteworthy strength’ citing the simple and intuitive graphical representation. B-10 also stated that “he has been in the business of producing ETO products for nearly 25 years and has not seen such a reasoned, thorough and rational presentation.” B-10 went onto say that it is possible to “easily envision using this framework as a basis for establishing a PLM programme and providing direction to my team.” The framework structure was also highlighted by B-12 as a strength stating that “the information, people, process and technology approach has allowed us to focus on the real areas of challenge in terms of PLM implementation, specifically cultural change and enabled processes.” The usefulness of the framework not just for ETO products but for other industries was raised by B-7 and B-9.
Finally, the importance of consideration of timescales for PLM implementation was highlighted by B-5 who stated: “Implementing a framework such as this takes a large amount of time, especially for a large organisation” and further linked the time aspect to the level of innovation by stating: “Any solution must be implementable in line with the business operating timescales and the rate of technological innovation.”
5.3. Industrial application of framework
BAE System Maritime Naval Ships has used the themes identified in the framework for the development of its PLM approach described in its integrated Bill of Materials (iBoM) strategy. This enabled PLM to support the objectives for the FoC new generation Royal Navy vessel and to overcome the characteristics related to production of ETO products as described in Section 1. The understanding of ETO products compared to other product types enabled BAE Systems Maritime Naval Ships to more broadly communicate the importance of PLM to achieve the objectives and how a specific approach to PLM is required. The iBoM strategy was also used to describe how this would enable their required design changes to be incorporated through variant management. The implementation of the themes in the strategy has established the business, as leaders in the field of PLM in Naval shipbuilding.
A key enabler from the framework was to create a dedicated cross-functional team who would be responsible for all aspects of PLM. Following the framework’s guidance, BAE Systems Maritime Naval Ships developed and implemented an innovative and transformational new organisational design named the PLM Capability Centre (CC). The PLM CC is a multifunctional Engineering, IM&T and Project Management CC for PLM on their global shipbuilding programmes. The PLM CC went live in February 2021 and consists of approximately 50 PLM specialists who deliver all aspects of PLM including vision and strategy, process development, people management and training, information policies, technology development and delivery and project management and support. The relationships between the PLM CC and the objectives, challenges and enablers are:
-
(i) provide single, clear accountability to deliver end-to-end PLM capability through a one-team approach (Section 4.3.1) to de-risk PLM delivery to programmes;
-
(ii) improve the utilisation of highly skilled scarce resources to improve the quality of delivery and value for money (Section 4.1.4) by ensuring that PLM SQEP resources are identified and applied to relevant business priorities;
-
(iii) improved organisational structure to recruit, develop, and retain niche PLM SQEP (Section 4.3.1);
-
(iv) reduce management overhead by integrating teams into a single PLM management structure (Section 4.3.3);
-
(v) greater transparency of PLM priorities, risk, dependencies, resource availability and skills, opportunities and plans to support programme objectives (Section 4.1.3);
-
(vi) remove both implicit and explicit barriers caused by PLM expertise within unintegrated teams (Section 4.3.1);
-
(vii) de-risk (Section 4.1.4) and improve PLM capability throughout the digital thread, that is not individual technologies such as CAD or PDM, but a fully integrated environment and
-
(viii) enable the strategy and policy development (Section 4.3.2), education and support for PLM.
The FoC new generation Royal Navy vessel has a number of electronic workflows that represent the PLM processes. These processes were rationalised to reflect the integrated PLM environment and cross-functional ownership. The workflows have a balance between complexity and simplicity and mirrors the varying degrees of complexity within the programme as advocated by the enabler described in Section 4.3.2. For instance, the current document review workflow in the PDM now reflects a straightforward and well-understood process that requires minimal management. These processes require to be extended for security, export and IPR obligations and to ensure that document management and publication meets the business objectives. The guidance in the framework must continue to be followed to ensure that these previously simple document management processes do not become overly complex. The change management workflows are more complicated due to the complexity of the programme with regard to uncertainty, emergent change and its relationship to configuration management. This requires a number of configured workflows that represent multiple activities and interactions across information, processes and stakeholders, including engineering, planning, manufacturing, finance, supply chain, programme management and the customer. Due to these complications, the workflows are managed centrally with a number of change managers supporting each of the functions to ensure that they are processed correctly. Guidelines and governance over process complexity must continue to be introduced to ensure that they are simple and usable, as described in Section 4.3.2. These processes must be mandated both within the business, across partners and the supply chain, as described in Section 4.3.3.
The standardisation of processes in ETO product development is challenging due to the bespoke highly customised nature of the product, as described in Section 1. The PLM environment can support these nonstandard activities by ensuring that the necessary process support is enabled where appropriate. Haug, Ladeby, and Edwards (Reference Haug, Ladeby and Edwards2009) argued that ETO organisations can move towards mass customisation by standardising aspects of their design and manufacturing, and Pulkkinen et al. (Reference Pulkkinen, Leino and Papinniemi2017) identified that there were significant opportunities for using PLM capability to transform bespoke ETO products into standardised processes more commonly seen in Assemble-to-Order products. To achieve a level of standardisation, the PLM business processes must be rationalised and governed. On the FoC new-generation Royal Navy vessel, the PLM implementation included rules that ensured that when the product artefacts are designed, consideration is made as to whether these can be standardised. An example is with the parts catalogue where a material is requested by engineering. The electronic workflows will force the engineer to reflect whether a standard material can be used, therefore assisting the supply chain team by reducing the variability of the material specifications and enabling economies of scale with larger orders. The workflow will also force the engineer to add a classification from a pick list of manufacturing processes, assisting the manufacturing engineering team to implement build environments that are based on the number of repeatable processes identified against the product artefacts. This will reduce the number of non-standard manufacturing processes since any identified will be targeted for removal where possible. Whilst the PLM processes, information, training and technology will support improvements in standardisation, there must be a manufacturing strategy that enables the realisation of the improvements through PLM. It also must be supported by the information polices to ensure that the BoM is targeted at the appropriate level, to ensure that the programme schedule is not impacted due to the enormity of the repeatable identification activities on large volumes of data.
6. Discussion
The framework shows that the processes on ETO products have specific objectives, challenges and enablers that are required for a successful PLM implementation within the development and delivery life phases. Quality through right first time and a reduction in rework is a process objective described earlier and in the demanded quality improvements to the FoC new-generation Royal Navy vessel. The production characteristics for ETO programmes described in Section 1 stated that there is no prototype to remove errors before manufacturing commences; therefore, right first-time quality is an important business objective.
Scheubel et al. (Reference Scheubel, Bierschneider, Gierse, Hermann and Wokusch2018), using the implementation of a new PLM system within the energy sector as a case study, stated that the implementation of PLM will enable process optimisation, process quality and will also lead to cultural change. They then described how a new PLM system could potentially introduce initial process overheads and result in opposition from the workforce. They added that these overheads would, however, be reduced through software improvements, training and enhanced skill levels. They also stated that enlarged electronic workflows increase process quality as they are increasingly developed to align with the business processes. Careful consideration must be given to enlarged electronic workflows as the thematic analysis identified how overly complex processes are a challenge in ETO implementation. The interviewees gave examples of how they had enlarged their electronic workflows, which eventually became unusable in the development of their ETO products. This led to the enabler to provide guidelines and governance over process complexity to ensure that they are simple and usable. The findings described how enlarging workflows and adapting them to the business process will actually reduce the effectiveness of the PLM environment, and will be detrimental to process quality. Integrating processes into larger workflows in the PDM system could benefit less-complex products. However, for ETO products, the size, complexity and uncertainty in the product development lifecycle results in a requirement for flexibility in the processes in order to adapt to the constant emergent changes. If the processes are too rigid and inflexible and these are reflected in the electronic workflows in the PLM environment, then these will prove ineffective and will result in a reengineering of the processes. The processes must not be overly complex; otherwise, they cannot be used effectively to support the PLM business objectives. A balance must therefore be struck between processes that are of sufficient quality to support the complex programme development, and those that are flexible enough to manage the uncertainty.
As illustrated in Figure 6 and described in Section 4.3.1, there is a need to develop a cross-functional team with suitable SQEP who will have PLM business process ownership, develop the processes and ensure that they are standardised across the business. The application of this key enabler into the structure of the business is described in Section 5.3 with the PLM CC.
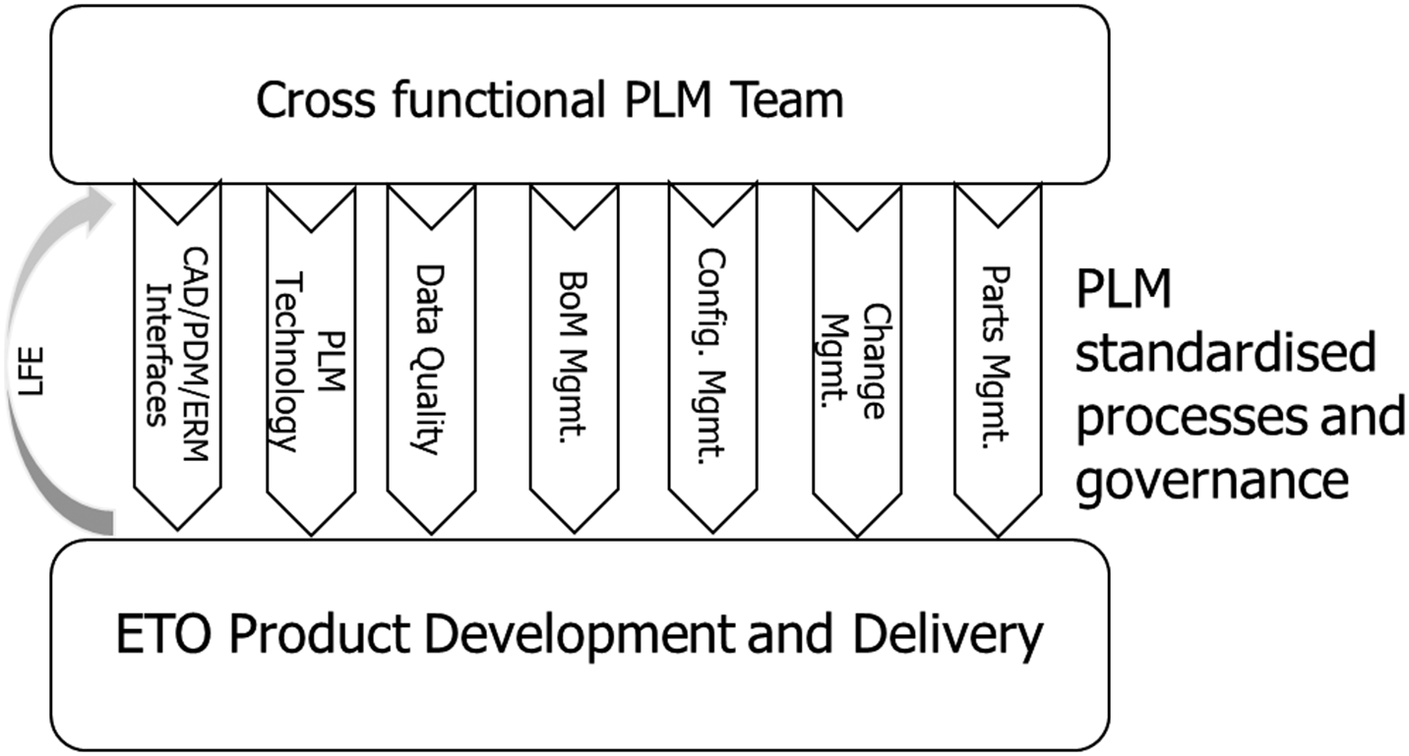
Figure 6. Cross-functional team for ownership and effective implementation of product lifecycle management processes.
The cross-functional PLM team also has the responsibility for LFE, and ensuring that the processes are adhered to. They lead on the guidelines and governance over process and complexity. The team should be cross-functional to ensure that each of the business functions has its needs represented, in turn assisting with the integration of processes across the organisation.
An example of process integration out-with the traditional functions such as engineering and supply chain are those required to support security, export and IPR objectives. Export increases complexity, not only in the extension of the management of information across potential variants of the product, but also with the processes the stakeholders must follow. Without cross-functional team representation from security, export and IPR, the processes used for NPD would be disparate from those required to meet the required legislation.
The UK Ministry of Defence (MoD) have recognised that whole life cost should include sustainable thinking in the delivery of defence capability. The consultancy KBR developed a ‘Roadmap for Sustainable Defence Support’ for the MoD in a drive to achieve zero carbon emissions by 2050. Initiatives that were identified in the report to achieve the associated targets include addressing: carbon emissions; fuel substitutes and technologies; circular economy, recycling and reduction in use and sustainability-enabling technologies. Delivering the same level of capability to the customer, to schedule and cost, whilst delivering zero carbon emission will influence the management of product lifecycle data and the associated PLM implementation, extending the Digital Thread further than current practice. This is likely to be of fundamental importance to providing a rational strategy for supporting circular economy in high-value ETO assets. It is conceivable, for example, that an additional circularity (or equivalent) baseline, or recyclable BoM, may be constructed in the future that supports this life phase. This is certainly a novel area for further research to fully explore the implications for PLM implementation to support sustainability within ETO product development.
This research has been undertaken on multi £B ETO programmes relating to PLM. Due to the scale of these programmes, it is not possible to describe all the details required to successfully implement PLM on ETO products. The framework provides guidance, and this can be augmented to assist in the successful implementation of PLM on ETO products. The results are bounded by the experts interviewed; however, the complexity of PLM on ETO products also provides a limit to the individuals who could describe the objectives, challenges and enablers. A comparison between other PLM implementation frameworks and the enablers within this has been developed by McKendry et al. (Reference McKendry, Whitfield and Duffy2022). The application context for most other implementation frameworks mainly relates to the MTS/MTO sectors. It was observed through this comparison that there was general consistency between the frameworks compared with process ownership through a dedicated functional team. However, the opposite was the case in relation to managing the process complexity, with very little mention of the importance in doing so, within other implementation frameworks. The mandatory utilisation of PLM processes was discussed by Bokinge and Malmqvist (Reference Bokinge and Malmqvist2012), but otherwise received very little consideration by other researchers.
7. Conclusion
The research presented here describes the need for the development of a framework to implement PLM on ETO products. Prior to this research, there existed no published guidance in relation to the considerations that a business should make in relation to tailoring the PLM implementation to address the complexities associated with ETO programmes. The scientific contribution of the research is the identification of the process-oriented factors that are instrumental in the successful implementation of PLM within an ETO context. For a PLM implementation to be successful in an ETO programme, there needs to be designed-in congruency between the PLM information, technology and processes to support the right first-time delivery of quality, schedule and cost.
The research introduced the characteristics of ETO programmes that reflect key differences to PLM implementation for ETO products as: high capital value; large scale; complex; long design and build lifecycle; long in-service life; no physical prototype; highly customised and few or one off. Twenty-seven semi-structured interviews were undertaken with senior PLM practitioners associated with 11 ETO product development programmes in the United Kingdom, France, Australia, the United States and Canada to elicit responses to 14 PLM implementation-related questions. As the interview questions related to PLM implementation objectives, challenges and enablers, this supported the development of the high-level design concept of the PLM implementation framework.
The development of the PLM implementation framework was primarily derived from the analysis of the interview responses in NVivo, but was also supported by literature where appropriate. The codes and themes developed in NVivo enabled the grouping of interview responses, allowing the related key points from the interviews to be described. The themes form the framework, and are grouped based on whether the interview question related to an objective, challenge or enabler and the themes of information, people, process and technology. The research presented here reflects the process objectives, challenges and enablers. Five process objectives were identified from the interviews: support the design and build for product safety and environmental considerations; enable quality through right first time and reduction in rework; enable product development and build collaboration across all stakeholders; cost, profit, risk reduction and value for money and enable standardised design and build. One process challenge was identified: creating processes that meet business objectives and are not overly complicated. Finally, three process enablers were identified from the interviews: PLM business process ownership, development, standardisation, LFW and adherence using suitable expertise within a dedicated cross-functional team; guidelines and governance over process complexity to ensure that they are simple and useable and mandate utilisation of PLM processes internally, to partners and the supply chain.
The main evaluation used questionnaires to ask selected participants from ETO products for their opinion on statements related to the framework. These participants were selected from multiple ETO organisations based on their relationship with PLM in ETO products either as an implementer or as a key stakeholder with an interest in its successful use within their organisation. The questionnaire responses supported the value of the framework for the implementation of PLM on ETO products. The industrial use of the framework themes in an ETO product also demonstrated its value, as findings from the research were used by BAE Systems Maritime to input into the Naval Ships PLM strategy.
The flexibility and scalability of the framework was identified as being important through the semi-structured interviews and with the evaluation questionnaires. The interviewees highlighted the importance of being able to pick and choose what element of the framework they wished to target. This would enable them to focus on areas that were a priority in their current lifecycle, or was identified a problem area within the organisation. The evaluation questionnaires provided evidence as to the value of the framework for the implementation of PLM on ETO products, for example, describing the framework as: “an invaluable asset to any business embarking on the implementation of PLM.”
Acknowledgments
This research would not have been possible if it was not for the commitment of all of those involved in providing thought-provoking and insightful responses to the interviewer’s questions, as well as agreeing to further validate the outcome of the analysis. Their contribution is very gratefully acknowledged.
Financial support
The authors would like to gratefully acknowledge the support and funding received from BAE Systems Maritime Naval Ships that allowed this research to be undertaken.