Hierarchical structures of materials: Origins of the idea
Starting from steel swords with complex structures to mud and straw-based buildings in Mali to ancient mortars and concrete, efforts to enhance the properties of materials by changing their structures have always been at the center of technological development. Composites, materials consisting of two or more dissimilar constituents with different properties, emerged from such efforts. While the possibilities of composite materials seemed infinite at first, two observations came into focus: (1) the composite constituents have their own, sometimes complex, structures that can in turn be modified, and (2) the potential for improving the properties of composite materials by adding or rearranging reinforcements is often limited—while some properties (e.g., stiffness) can be improved by increasing the volume content of hard reinforcements, other properties (e.g., fracture toughness) degrade. This motivated modifications of structure and properties of composite constituents and their control at several scale levels. Reference Kanzaki, Shimada, Komeya and Tsuge1
At the same time, the extraordinary properties of materials found in nature, including wood, nacre, bone, and other biological materials, attracted the interest of the scientific community. It was observed that one of the main sources of such extraordinary properties of biocomposites is their complex hierarchical structure. In his classic paper, Lakes Reference Lakes2 summarized the main ideas of hierarchical materials as a “basis for synthesizing new microstructures, which give rise to enhanced or useful physical properties.” This provided the impetus for the development of new, bioinspired materials based on biomimicry principles. Reference Fratzl and Harrington3 With the continuing advances and development of nanotechnology, new possibilities emerged to enable the manufacture of hierarchical materials with constituents modified on the nanoscale.
Biological hierarchical materials: Variety of structures and biomimicking
Natural biological materials often demonstrate extraordinary strength, damage resistance, and hardness. For instance, nacreous mollusk shells, which consist of 95% CaCO3 by volume, have double the strength and exhibit a work of fracture that is 3000 times higher than that of monolithic CaCO3. Reference Rao4 Numerous studies have been devoted to the analysis of the sources of such extraordinary properties of biological materials. Several features have been identified, including the staggered brick-and-mortar structure and interlocked platelets of nacre (see Figure 1 ), Reference Sarikaya5–Reference Xu and Zhang8 the layered structure with randomly distributed layer thicknesses found in the spicules that provide structural support in certain sea sponges, the functionally graded structures (graded distributions of reinforcement) of bamboo Reference Amada, Ichikawa, Munekata, Nagase and Shimizu9 and tooth, Reference Yilmaz, Schneider and Swain10 and features of wood such as a cellular multilayered structure and fiber/fibrils with varied distribution and density. Reference Qing and Mishnaevsky11 In most cases, biological materials are hierarchical materials, with varied but still complex (lamellar, cellular, staggered, porous) structures at multiple scale levels. In their article in this issue, Weinkamer and Fratzl provide a more detailed overview of the structures and properties of natural hierarchical materials.
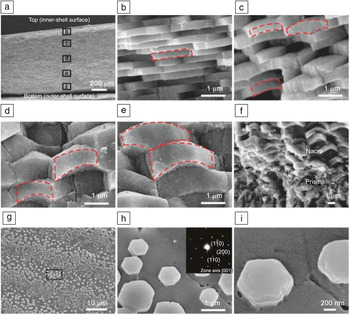
Figure 1. Nacre at nanoscale level—scanning electron micrographs showing cross-sectional views and a plane view at the shell center. (a) Full view of a cross-sectional slice. (b–f) Detailed views of the corresponding marked areas in (a). (g) Full view of the inner surface at the shell center. (h) Detailed view of the labeled area in (g). (i) Enlarged view of (h). The areas marked in (b–e) highlight some typical platelet shapes. Reprinted with permission from Reference Reference Xu and Zhang8. © 2015 Elsevier.
The connection between the extraordinary performance of biological materials and their hierarchical structure motivated research toward new man-made materials using the same principles. Reference Studart, Erb, Libanori, Kim, Randow and Sano12 Tough and strong alumina ceramic-based materials with a nacre-like brick-and-mortar structure have been made using freeze-casting of nanoparticle suspensions. Reference Bouville, Maire, Meille, de Moortele, Stevenson and Deville13 Polyurethane-based composites for stretchable electronics were developed using solvent-based hierarchical reinforcement approaches, with nanoclay and inorganic particles distributed in a polyurethane matrix. Reference Libanori, Munch, Montenegro and Studart14 Materials with hierarchical porous structures (such as sponges or bone) demonstrate high permeability and surface area and can be used in catalytic and gas-adsorption applications. Other applications of materials with hierarchical porosity are bone implants (improving osteointegration of implants, thanks to large pores) and materials for impact protection. Such materials can be produced by templating or three-dimensional (3D) printing. A special case of bioinspired hierarchical materials is materials with hierarchical surface topography (e.g., adhesives inspired by gecko feet), and antifouling and self-cleaning surfaces that mimic shark skin and lotus leaves. Reference Liu and Jiang15
Interface to biological tissues: Hierarchical materials for medical applications
The biomimetic roots of hierarchical materials and their structural similarity to biological tissues suggested medical uses (implants, hard-tissue engineering, and drug delivery) as one of their first application areas. Attributes required for materials used in medical implants include biocompatibility and mechanical properties similar to those of bone, such as porosity and osteoconductivity (the ability to provide templates for new bone formation). Several groups are developing hierarchical materials with structures similar to those of hard tissues, including 3D structures of inorganic mineral plates and organic matrices. Reference Kumar, Agrawal, Lahiri, Kim, Randow and Sano16 Ceramic-based hierarchical composites with bioactive calcium phosphate derivatives and bioglass using organic synthetic polymers (collagen, celluloses, gelatin) have been developed for bone-tissue engineering applications.Reference Furuichi, Oaki, Ichimiya and Imai17 Nano-hydroxyapatite collagen composites have structures similar to that of bone and show excellent bioactive and biodegradable properties. Reference Du, Cui, Zhu and de Groot18 Mesoporous bioactive glasses produced by 3D printing with polymer addition have a hierarchical pore structure and demonstrate good mineralization ability as scaffolds for bone regeneration. Reference Luo, Wu, Lode and Gelinsky19
For hierarchical drug-delivery materials, requirements include the ability for controlled drug release combined with mechanical strength and biodegradability. Hierarchical composites with multiscale porous architectures can meet these requirements. Hierarchical porous composites with CaCO3 and polymer hybrids obtained via self-assembly biomineralization have enabled controlled release for cancer treatment. Reference Shi, Qi, Du, Shi and Cao20 The importance of hierarchical materials for medical applications is related to the fact that medical materials interact directly with the biological tissues and are subject to the same service conditions; similar requirements dictate similar structures in this case.
Strong and tough materials: Enhancing performances beyond limits
A typical example of conflicting materials properties is the desire for combined high strength and toughness—if a material is reinforced with stiff particles, its strength and stiffness tend to grow with increasing reinforcement content, but the toughness might be reduced. This challenge can be overcome by using hierarchical structures. Kanzaki et al. Reference Kanzaki, Shimada, Komeya and Tsuge1 developed an alumina-based ceramic material within the framework of the Japanese “synergy ceramics projects” with both high strength and toughness, achieved by a combination of aligned anisotropic grains (at microlevel) with the intragranular dispersion of nanoparticles (at nanolevel).
Another example of managing conflicting or competing properties is that of unidirectional fiber-reinforced polymer composites. These lightweight and strong materials are used in wind-energy applications, Reference Mishnaevsky, Brøndsted, Nijssen, Lekou and Philippidis21,Reference Mishnaevsky22 structural engineering, and the automobile industry. While the fiber reinforcement ensures excellent tensile stiffness and strength of the composites, their fatigue resistance and compressive strength (important factors, among others, for wind-energy applications) need some improvements. The addition of a small amount of nanoparticles (carbon nanotubes, graphene, or nanoclay) in the epoxy polymer matrix or fiber/matrix interface (fiber coating, so-called sizing) of the composites allows their fatigue lifetime to be increased by several times (see Figure 2 ). Reference Mishnaevsky and Dai23

Figure 2. 3D computational model of fiber-reinforced polymer composites with secondary nanoparticle reinforcement. Reprinted with permission from Reference Reference Mishnaevsky and Dai23. © 2014 Elsevier. Note: CNT, carbon nanotube.
Biosensors used to detect analytes in the body (e.g., blood glucose) rely on hierarchical polymer structures that ensure higher surface area and faster diffusion of molecules. Reference Zhao, Liu, Pan and Yu24 For example, 3D hierarchically porous polyaniline hydrogels have been used in new enzyme-based glucose sensors. Reference Pan, Yub, Zhai, Ryoung Lee, Zhao, Liu, Wang, Tee, Shi, Cui and Bao25 In their article, Gorbatikh et al. discuss in greater detail the applications of hierarchical structures for property enhancements of lightweight polymers. Sidorenko et al. further discuss the application and potential of hierarchical materials in machining technologies in their article in this issue.
Hierarchical materials for energy storage and conversion, adsorption, and catalysis: Transport and diffusion properties
Important areas of the application of hierarchical materials include energy storage and conversion. The electrochemical properties of materials can be greatly enhanced by using materials with hierarchical structures, which can provide larger surface areas for interfacial diffusion, transport, and reactions. This opens new possibilities for the development of materials with improved electrical conductivity, facilitated diffusion paths, and electrolyte migration for applications such as electrode scaffolds and catalyst supports. Reference Zhao, Peng, Yu, Kim, Randow and Sano26 Efforts have been made to develop hierarchical carbon-based nanocomposites for the electrodes of electrochemical supercapacitors. Due to their large surface area, open porosity, and high conductivity, these materials ensure improved energy densities for these devices. For lithium-ion batteries, using hierarchical materials as anodes allows reduction of the diffusion path of lithium ions and also accommodates volume changes due to alloying/dealloying.
In fuel-cell applications, using hierarchical nanostructured carbon as the cathode catalyst in polymer electrolyte fuel cells achieves enhanced catalytic activity for oxygen reduction and improved overall cell performance, Reference Shi, Qi, Du, Shi and Cao20 while hierarchically porous chitosan/graphene composites as anodes deliver good power densities. Reference He, Liu, Qiao, Li and Tan27
For materials used as adsorbents and catalysts, hierarchical organization of porosity at the micro-, meso-, and macrolevel can impact performance characteristics such as activity, selectivity, and stability. Reference Mitchell, Pinar, Kenvin, Crivelli, Kärger and Pérez-Ramírez28 In his article, Snyder discusses various synthesis strategies based on direct synthesis, post-synthetic modifications, and combinations thereof that are being developed. In their article, Valtchev and Mintova discuss hierarchical zeolites (ordered microporous materials incorporating meso- and macropores) that find uses in industrial applications such as crude oil cracking catalysts. Reference Zhao, Peng, Yu, Kim, Randow and Sano26 A major motivation for hierarchical organization of porosity is to control molecular traffic in order to reduce diffusion limitations or improve selectivities. In addition, hierarchy in catalytic activity can be accomplished by selective placement of catalytic centers at distinct pore environments, enabling cascade reactions. Reference Parlett, Isaacs, Beaumont, Bingham, Hondow, Wilson and Lee29
Computational modeling
The main directions for computational modeling of hierarchical materials and structures include the analysis of interactions and synergies between scales (i.e., hierarchical load sharing), Reference Mishnaevsky30 analysis of multiphysics and multiple functionality aspects of hierarchical materials, direct microstructure-based simulations, Reference Mishnaevsky31 and analysis of nanoscale effects of materials behavior.
One approach to simulating the hierarchical structures of materials is based on hierarchical load-sharing models. According to this approach, the load is transferred from the larger-scale structures (“roots”) of the hierarchical “tree” to the lower “branches” and down to the smallest elements of the material (e.g., fibers, in the case of long fiber-reinforced composites). Reference Parlett, Isaacs, Beaumont, Bingham, Hondow, Wilson and Lee29 The load is shared equally among all of the sub-elements of a given branch (as long as they are intact) or among remaining intact sub-elements after some of them fail. Such models allow the effects of hierarchical structures and hierarchical load transfer to be analyzed in their pure form, as they only address the hierarchical structures.
Another more detailed modeling approach is based on direct numerical multiscale modeling of each structural level. In this case, wood is modeled as a cellular material, with multilayered walls and various nanoscale structures in each wall layer. Reference Qing and Mishnaevsky11 Hierarchical nanoreinforced composites are also modeled as multilevel materials, with microscale and nanoscale reinforcements. Reference Mishnaevsky22 The main computational challenges in such models are the large gap between scales, the high-aspect ratio of reinforcements (such as carbon nanotubes or graphene), and the strong nonlinearity of the material behavior, all requiring additional computational resources.
A review of the modeling techniques used for hierarchical materials is given in the article by Signetti et al. in this issue.
Hierarchical materials: Summary and perspectives
Materials with hierarchical structures represent a promising approach to enhance performance far beyond what can be achieved using composite structures, to add new functionalities and to adapt to special requirements (such as osteoconductivity in implantology).
The idea of mimicking biological materials provided the first impetus to the development of materials with hierarchical structures. Current directions for the development of hierarchical materials are more goal oriented. In many cases, structures at different scale levels play different, complementary roles, and ensure different functionalities for multifunctionality applications. Development of nanoscale technologies capable of delivering the required nanoscale structures (building blocks) and corresponding properties is a major prerequisite. Manufacturing by organizing nanoscale building blocks (polymer chains, macromolecules, nanoparticles) into structures is the main challenge for hierarchical materials development. A promising direction for overcoming this challenge is the spontaneous organization (self-assembly) of the building blocks into the required structures driven by physical or chemical mechanisms. Reference Whitesides and Grzybowski32,Reference Whitesides and Boncheva33
The articles in this issue overview the state-of-the-art of aspects related to the analysis and development of hierarchical materials. Using biomaterials and multiscale modeling as starting points, we seek to enhance the performance and add new functionalities to hierarchical materials for lightweight structural and energy applications, catalysis, and machining of materials.