Introduction
Palmer amaranth is the most troublesome weed in many U.S. crops (Van Wychen Reference Van Wychen2019, Reference Van Wychen2020). This weed grows 0.18 to 0.21 cm growing degree d−1 and reaches more than 2 m tall (Horak and Loughin Reference Horak and Loughin2000; Sellers et al. Reference Sellers, Smeda, Johnson, Kendig and Ellersieck2003). Palmer amaranth is difficult to manage because one female plant reaching maturity can produce 200,000 to 600,000 seeds plant−1 (Keeley et al. Reference Keeley, Carter and Thullen1987; Sellers et al. Reference Sellers, Smeda, Johnson, Kendig and Ellersieck2003; Sosnoskie et al. Reference Sosnoskie, Webster, Grey and Culpepper2014). In addition, resistance to eight herbicide modes of action and individual populations with up to five-way multiple resistance have been reported in Palmer amaranth growing in the United States (Heap Reference Heap2021).
Sweetpotato, peanut, and cucumber are economically important crops in North Carolina that produce canopies 0.5 m or lower in height, resulting in low competitive ability with Palmer amaranth for light. Eighty percent of Palmer amaranth leaf area occurs above 1 m (Massinga et al. Reference Massinga, Currie and Trooien2003) and can intercept up to 84% of light above 0.5 m (Moore et al. Reference Moore, Jennings, Monks, Boyette, Jordan and Leon2021). Competition from Palmer amaranth has reduced yield by up to 98% in cucumber (McGowen et al. Reference McGowen, Jennings, Chaudhari, Monks, Schultheis and Reberg-Horton2018), 68% in peanut (Burk et al. Reference Burk, Schroeder, Thomas and Wilcut2007), and 95% in sweetpotato (Barkley et al. Reference Barkley, Chaudhari, Jennings, Schultheis, Meyers and Monks2016; Basinger et al. Reference Basinger, Jennings, Monks, Jordan, Everman, Hestir, Waldschmidt, Smith and Brownie2019; Smith et al. Reference Smith, Jennings, Monks, Chaudhari, Schultheis and Reberg-Horton2020). In North Carolina, sweetpotato is the third most economically important crop, accounting for US$375 million annually (USDA-NASS 2021). Annually, peanut and cucumber account for US$92 and US$19 million, respectively, in North Carolina (USDA-NASS 2021).
Though low-growing crops are not competitive against Palmer amaranth, the difference in height between the crop and the weed provides options for selective control. Wick/wiper-applied nonselective herbicides can control tall Palmer amaranth, though herbicide contact with crop foliage can cause unacceptable injury (Meyers et al. Reference Meyers, Jennings, Schultheis and Monks2016, Reference Meyers, Jennings and Monks2017). Mowing weeds over the crop canopy can reduce light interference, but Palmer amaranth will regrow and produce seeds (Finney et al. Reference Finney, Creamer, Monks, Jennings and Mitchem2008; Sosnoskie et al. Reference Sosnoskie, Webster, Grey and Culpepper2014). The Bourquin Organic Weedpuller (Bourquin Design and Manufacturing, Colby, Kansas, USA) uses rubber tires and notched disk plates rotating in opposite directions from adjacent tires at a 30° upward angle from vertical to grab and uproot weeds growing taller than the crop (Figures 1 and 2). In soybean [Glycine max (L.) Merr.] and adzuki bean [Vigna angularis (Willd.) Ohwi & Ohashi] that were approximately 0.8 m at treatment, control of common ragweed (Ambrosia artemisiifolia L.), common lambsquarters (Chenopodium album L.), and redroot pigweed (Amaranthus retroflexus L.) was less than 50% with three passes of the Weedpuller, and injured weeds still produced viable seeds (Simard et al. Reference Simard, Page and Nurse2019). However, it is possible that utilization in shorter crops could improve efficacy if weeds are treated before extensive root expansion.
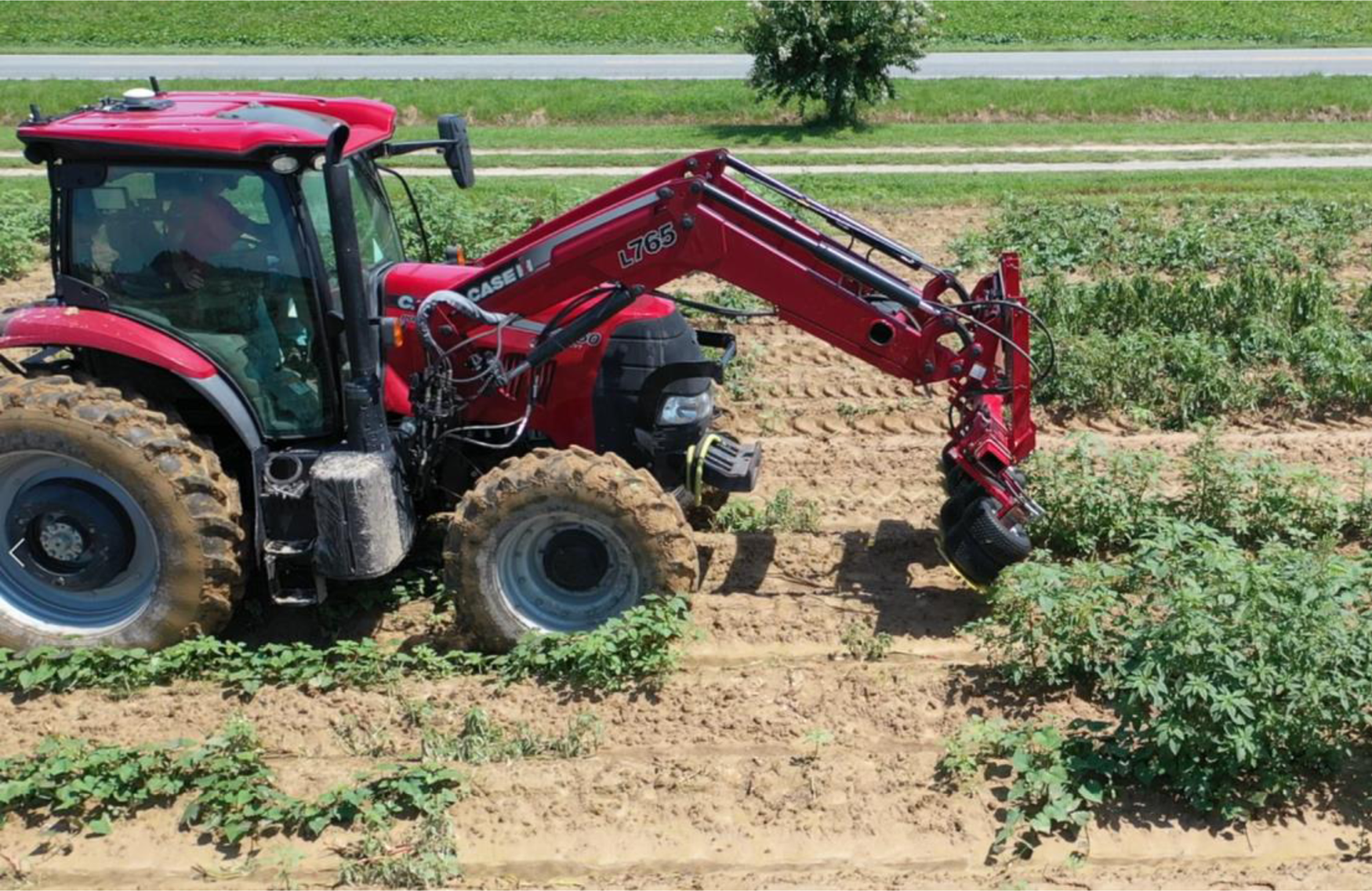
Figure 1. The Bourquin Organic Weedpuller/roguing machine–Posi Pull mounted onto a front-end tractor-mounted loader.
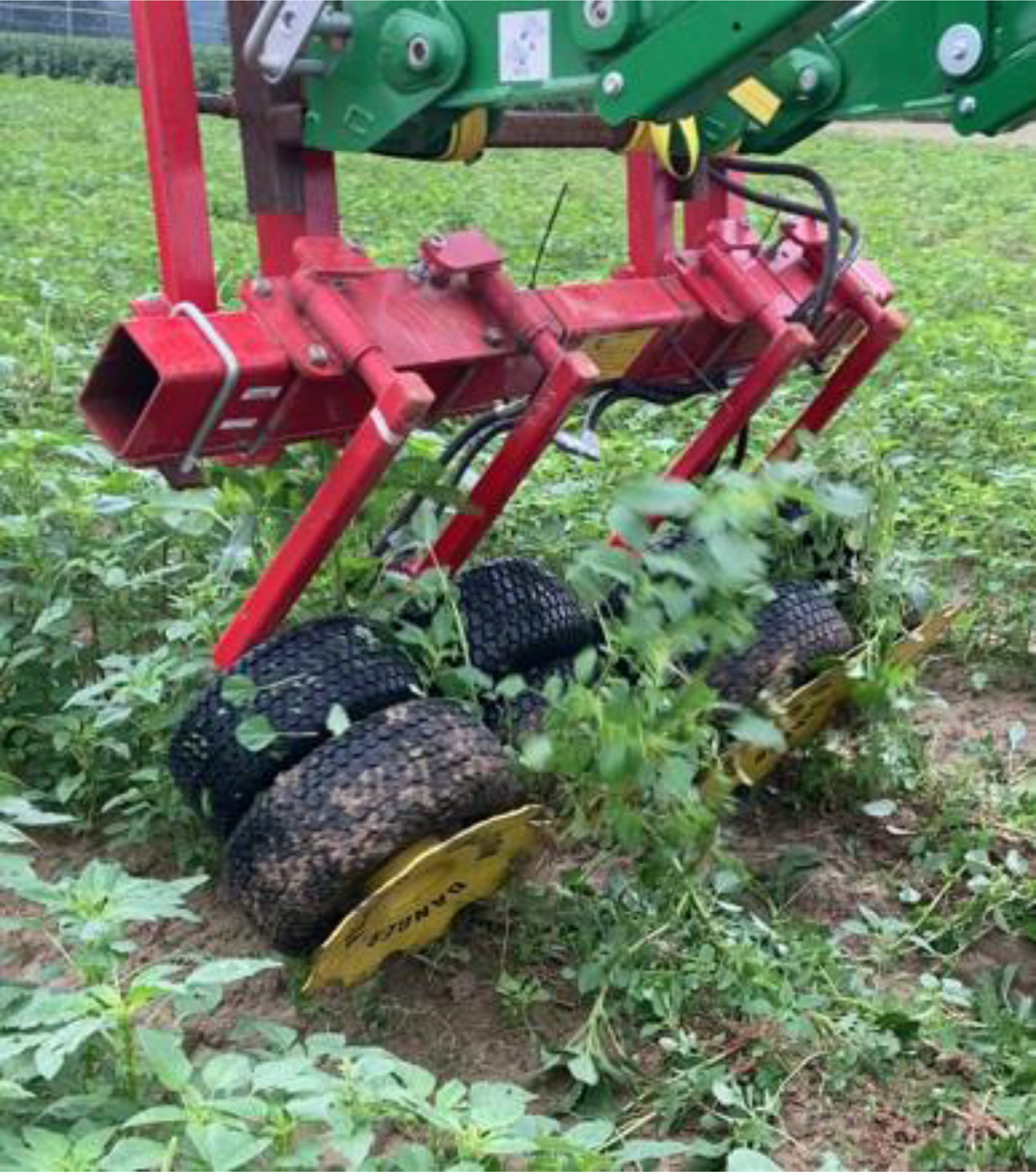
Figure 2. The Bourquin Organic Weedpuller/roguing machine–Posi Pull removing rows of weeds.
The Lasco Lightning Weeder (Lasco Lightning Weeder, Ottertail, MN, USA) and the Weed Zapper (Old School Manufacturing, Sedalia, MO, USA) (Figure 3) are two commercially available options that use electricity to control weeds overtopping crops. Electricity applied at high voltage will heat and rupture plant cells, leading to desiccation (Ascard et al. Reference Ascard, Hatcher, Melander, Upadhyaya, Upadhyaya and Blackshaw2007; Diprose and Benson Reference Diprose and Benson1984). Electrical weed control can be achieved in a field using a power take-off (PTO)-driven generator and a step-up transformer that sends electricity to an electrode mounted on the front or back of the tractor. Once the electrode comes into contact with a plant that is separated by height or location from the crop, the electricity will pass through the plant, into the soil, and back to the generator through grounding disks or earthing wheels attached close to the electrode (Ascard et al. Reference Ascard, Hatcher, Melander, Upadhyaya, Upadhyaya and Blackshaw2007). Field equipment used for electric weed control typically applies 50 to 200 kW at 6 to 25 kV (Ascard et al. Reference Ascard, Hatcher, Melander, Upadhyaya, Upadhyaya and Blackshaw2007).
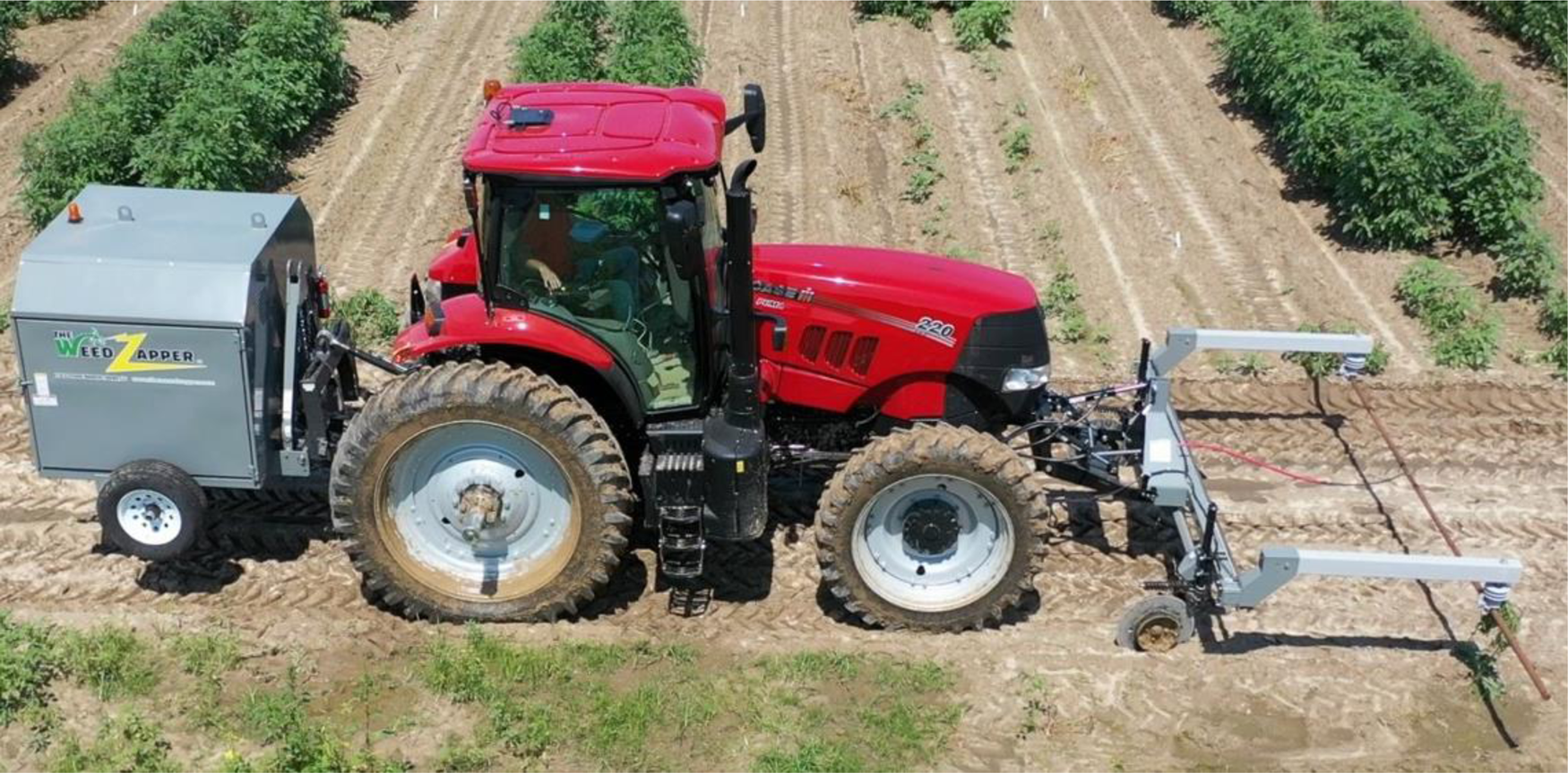
Figure 3. The Weed Zapper Annihilator 6R30 mounted onto a Case IH 220 tractor.
Diprose et al. (Reference Diprose, Benson and Willis1984) provided an extensive review of the efficacy of electricity in controlling weeds. The energy and voltage, duration of contact, density of weeds, and soil moisture will affect weed control (Diprose et al. Reference Diprose, Benson and Willis1984). In addition, weeds differ in the amount of electricity required for control, and all weeds evaluated required more energy as maturation progressed (Diprose and Benson Reference Diprose and Benson1984). Weeds with large root systems, such as many perennial grasses, are more difficult to control (Ascard et al. Reference Ascard, Hatcher, Melander, Upadhyaya, Upadhyaya and Blackshaw2007; Diprose and Benson Reference Diprose and Benson1984). Plants that come into contact with high-voltage electricity are typically controlled; however, many weeds may escape the application because of their short stature. Wilson and Anderson (Reference Wilson and Anderson1981) reported 50% redroot pigweed control after three passes in sugar beet [Beta vulgaris (L.)] using the Lasco Lightning Weeder.
Both conventional and organic cropping systems can benefit from effective physical weed management. Reed (Reference Reed2009) stated that suitable herbicides will always outperform electrical weed control with regard to cost and effectiveness, but the number of available herbicides is continually being reduced in the United Kingdom, where the author was located. In certified organic crop production, nonsynthetic herbicides are allowed only if nonchemical measures fail to provide adequate control. They are often expensive, with limited efficacy. As a result, weed management is often reliant on cultivation and hand removal (S. C. Smith and LDM, unpublished data). However, hand removal is expensive and labor intensive. Thus studies were conducted to compare electrical and mechanical methods and hand roguing for Palmer amaranth management in cucumber, peanut, and sweetpotato. In addition, growers currently utilizing electricity for weed management have inquired if treatments have effects on seed production or viability in addition to the effects caused by plant mortality. Thus additional studies were conducted to determine the effects of electrical treatments on Palmer amaranth seed production and viability.
Materials and Methods
Palmer Amaranth Management
Field studies were initiated at the Horticultural Crops Research Station (35.023°N, 78.280°W) near Clinton, NC, in 2020 and 2021 in fields with historically high Palmer amaranth densities (50 to 100 plants m−2). ‘Maxi Pick’ pickling cucumber, ‘Walton’ Virginia-type peanut, and ‘Covington’ sweetpotato were planted into independent studies each year. Cucumbers were overseeded and thinned to a 15-cm in-row spacing, peanuts were seeded to a 6-cm in-row spacing, and nonrooted sweetpotato cuttings were transplanted to a 30-cm in-row spacing in July of each year. Rows consisted of raised beds spaced 1 m apart, and plots were 6 m long. The soil was an Orangeburg loamy sand (fine-loamy, kaolinitic, thermic Typic Kandiudult) with a pH of 6 and 1% organic matter for sweetpotato and cucumber in 2020, a Norfolk loamy sand (fine-loamy, kaolinitic, thermic Typic Kandiudult) with a pH of 5.5 and 0.5% organic matter for peanut in 2020, and a Norfolk loamy sand with a pH of 6 and 0.5% organic matter in 2021. Soil fertility was maintained at levels sufficient for each crop, and overhead irrigation was applied as needed.
The experimental design for each study was a randomized complete block with treatments replicated four times. Cucumber and peanut plots consisted of four rows spaced 1 m apart and 6 m long; the two center rows were planted and used for data collection, and the two outside rows were not planted. Sweetpotato plots consisted of five rows, spaced 1 m apart and 6 m long, where the first four rows were planted and treated, and only the two center rows were used for data collection; the fifth row was not planted. Treatments were arranged in a 3 × 4 factorial where the first factor included a treatment method of electrical (Figure 3) (Weed Zapper Annihilator 6R30, Old School Manufacturing), mechanical (Figures 1 and 2) (Bourquin Organic Weedpuller/roguing machine–Posi Pull, Bourquin Design and Manufacturing), or hand-roguing Palmer amaranth control, and the second factor consisted of treatments applied when Palmer amaranth was approximately 0.3, 0.6, 0.9, or 1.2 m above the crop canopy. The Weed Zapper was set to the first pass broadleaf setting and powered by a Case IH Puma 220 (190 PTO horsepower) (CNH Industrial America, Racine, WI, USA) at 2,200 engine rpm and 3.5 km h−1. Control with the Weedpuller was implemented at 1.5 km h−1 with the wheels rotating at 25 rpm. After each initial treatment, additional treatments were applied if successive weeds reached the assigned height. A nontreated weedy plot was included in each block for comparison. The nonplanted rows within a plot were used to ensure that the adjacent plots did not contact the 15-ft Weed Zapper electrode. All crops were planted into 1-m-wide rows because of available tractor tire spacing. Interrow weeds were controlled using cultivation, and clethodim 135 g ai ha−1 (Select Max, Valent USA, Walnut Creek, CA, USA) was applied to the entirety of the study areas for annual grass control.
Effects of treatments on Palmer amaranth control were evaluated using a scale of 0% (no control) to 100% (plant mortality) (Frans et al. Reference Frans, Talbert, Marx, Crowley and Camper1986). Percent crop mortality was calculated by dividing the difference between the number of plants counted before the first treatment application and the number counted at the end of the growing season by the number of plants counted before the first treatment application. Sweetpotato crop stand could not be accurately counted at the end of the growing season because of between-row cultivation burying vines. Peanuts were dug and inverted 16 wk after planting (WAP). Because of a late peanut planting and limited equipment and personnel availability in 2020 owing to COVID-19 restrictions, peanut pod counts were used to assess the yield response. Sweetpotato storage roots were harvested using a chain digger 16 WAP; hand sorted into canner (>2.5 to 4.4 cm diameter), no. 1 (>4.4 to 8.9 cm diameter), and jumbo (>8.9 cm diameter) grades (USDA 2005); and weighed. Total yield was calculated as the sum of all grades.
Data were assessed for homogeneity of variance by examining residual plots. Arcsine square root transformations were required for Palmer amaranth control data. Back-transformed least-squares means were presented. Analysis of variance (ANOVA) was conducted using proc glimmix (SAS version 9.4, SAS Institute, Cary, NC, USA). For Palmer amaranth control data, fixed effects included application method, application timing, and their interactions, whereas study, all interactions including study, and replication nested within study were considered random effects. For crop data, fixed effects included year, application method, application timing, and their interactions, whereas replication nested within year was considered a random effect. When significant interactions were present, a slice statement was used to evaluate simple effects within the interaction (Littell et al. Reference Littell, Milliken, Stroup and Wolfinger1996). Least-squares means were separated according to Tukey–Kramer honestly significant difference (α = 0.05).
Seed Production and Viability
Raised beds spaced 1 m apart were prepared in July 2020 and July 2021 at the Horticultural Crops Research Station near Clinton, NC. The soil was an Orangeburg loamy sand (fine-loamy, kaolinitic, thermic Typic Kandiudult) with a pH of 6 and 1% organic matter in 2020 and a Norfolk loamy sand with a pH of 6 and 0.5% organic matter in 2021. Natural populations of Palmer amaranth were thinned to approximately 50 plants m−2 using between-row cultivation. The study was arranged in a randomized complete block design with four replications. Plots consisted of four rows, each 3 m long. Treatments consisted of electricity applied to Palmer amaranth at first visible inflorescence, 2 wk after first visible inflorescence (WAI), or 4 WAI using the Weed Zapper Annihilator as previously described. In addition, check plots, which were treated the same as other plots, only without the generator (electricity) turned on, were included for comparison.
Five gynoecious plants per plot were harvested immediately after application. In addition, plots from the first application stage were harvested 2 and 4 WAI, and plots from the second treatment stage were harvested 4 WAI. At the last treatment timing (4 WAI), plants in the nonelectrically treated check were large and at reproductive maturity; thus plots previously treated and the check were harvested before the last treatments were applied to avoid seed shatter. After the 4 WAI treatment, the nonelectrically treated check was harvested again for comparison.
Plots were threshed using a mill (Thomas Scientific, Swedesboro, NJ, USA), and seeds were separated from floral material using a vertical air column separator and stored at 4 C and 25% relative humidity. Seed production was estimated by multiplying the number of seeds in 1-g subsamples from each plot by the total plot weight. Four months after being placed in cold storage, 30 mature (black) seeds per plot were placed into 10-cm-diameter petri dishes containing filter paper moistened with 10 ml water, sealed with parafilm, and placed back into cold storage for 4 wk to overcome dormancy. Then the petri dishes were placed into a germination chamber at a 16-h photoperiod set to 35/25 C day/night and 100% relative humidity for 3 d. Germinated seeds were counted, then seedlings (radicle and hypocotyl) were imaged using a flatbed scanner (Expression 10000 XL, Epson America, Long Beach, CA, USA). Seedlings were arranged to avoid overlapping during scanning. Root measurement image analysis software (WinRHIZO, Regent Instruments, Quebec, QC, Canada) was used to measure total seedling length. Average seedling length was calculated by dividing the total length of seedlings by the number of germinated seeds in each plot. Seed viability was assessed on 30 seeds plot−1 using a crush test (Sawma and Mohler Reference Sawma and Mohler2002).
Residual plots were assessed for normality and homogeneity of variance. Data were subjected to ANOVA using proc mixed (SAS version 9.4). Treatment timing was considered a fixed effect, and replication was treated as a random effect. Dunnett’s test was used to compare treatments to the respective nonelectrically treated check (α = 0.05).
Results and Discussion
Palmer Amaranth Control
Treatment method by application height interactions were present for each evaluation timing (P < 0.0001); thus the simple effects of treatment method were assessed by application height (Table 1). After treatment, Palmer amaranth that were not tall enough to be controlled and plants that were not fully controlled continued to grow. Thus four weekly and two treatments, spaced 2 wk apart, were required for the 0.3- and 0.6-m application height, respectively, though only one treatment was required for the 0.9- and 1.2-m application heights. Schreier et al. (Reference Schreier, Bish and Bradley2022) also observed increased weed control from multiple passes with the Weed Zapper. Hand weed removal consistently resulted in optimal weed control. Four WAT, the electrical applications controlled Palmer amaranth at least 27 percentage points more than the mechanical applications when applied at the 0.3- and 0.6-m timings. With both the 0.9- and 1.2-m application timings, electrical and mechanical applications controlled Palmer amaranth by at most 87% by 4 WAT. When weeds were small, the Weedpuller would grab and uproot only weeds that had greater separation in height from the crop, whereas the electrical applications could control weeds that were closer to the crop in height. Once the weeds became larger, the electrical applications were less effective because of the increased weed biomass that needed to be treated. This is contrary to previous research, which reported electrocution to be more effective at later plant growth stages (Schreier et al. Reference Schreier, Bish and Bradley2022).
Table 1. Influence of treatment method and application height on Palmer amaranth control. a, b, c, d

a Data are pooled across years and crops.
b Means within a column for dependent variables followed by the same letter are not significantly different according to Tukey–Kramer honestly significant difference (α = 0.05).
c Abbreviation: WAT, wk after treatment application.
d Rating scale: 0%, no treatment effect; 100%, plant mortality.
e Treatments were applied using the Weed Zapper Annihilator 6R30 for electrical control and the Bourquin Organic Weedpuller/roguing machine–Posi Pull for mechanical control.
Under ideal conditions, weeds should be removed before overtaking the crop in height to reduce competition for light. In sweetpotato, the critical period of weed removal occurs when weeds are close to the same height as the crop (S. C. Smith, personal communication, 2021). However, in organic production with the absence of preemergence herbicides, intrarow weeds that escape cultivation are often not hand removed until they are greater than or equal to the height of these low-growing crops. The lowest treatment timing of Palmer amaranth 0.3 m above the crop canopy was selected based on when the mechanical control could grab and uproot the weeds without damaging the crop; however, the electrical and hand-removal options could be initiated earlier.
Crop Mortality
Palmer amaranth densities were high (50 to 100 plants m−2), thus cucumber were actively damaged or uprooted, with the hand-removal plots maintaining only 50% stand after treatment (Table 2). As cucumber was shaded by Palmer amaranth, crop plants responded with etiolation, causing long plants that grew upward with the weeds. The tendrils grabbed on to the Palmer amaranth, further increasing the difficulty of weed removal. In a typical field situation, because of the absence of herbicides in these high densities of Palmer amaranth, this cucumber crop would likely be a complete loss, as the cost to remove weeds with the care needed to prevent crop damage would be high. The use of mechanical and electrical weed control further increased crop mortality by at least 14 percentage points compared to the hand removal.
Table 2. Influence of treatment method and application height on cucumber and peanut mortality. a, b, c
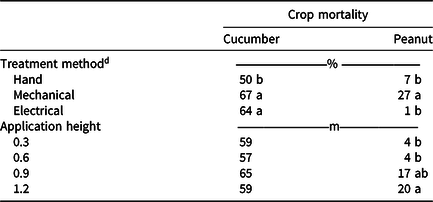
a Data are pooled across years.
b Means within a column for dependent variables followed by the same letter are not significantly different according to Tukey–Kramer honestly significant difference (α = 0.05). Means within a column not followed by a letter are not significantly different according to a nonsignificant F statistic (P > 0.05).
c Rating scale: 0%, no treatment effect; 100%, plant mortality.
d Treatments were applied using the Weed Zapper Annihilator 6R30 for electrical control and the Bourquin Organic Weedpuller/roguing machine–Posi Pull for mechanical control.
Peanut mortality was greatest when the Weedpuller was used for Palmer amaranth control. However, the Weed Zapper and hand removal each caused less than 7% peanut mortality across treatment heights. When treatments were applied at the 0.3- and 0.6-m weed heights, peanut mortality was 4% across treatment methods. At the 1.2-m treatment height, 20% peanut mortality was observed.
Yield
Cucumber yield was suboptimal owing to unfavorable environmental conditions, resulting in heat and water stress and in disease. Cucumber plots had less than 0.3 fruit plant−1 in the highest-yielding plots; thus data were not presented. Owing to a significant treatment method by application height interaction for peanut pod count and total sweetpotato yield (P < 0.05), data were assessed by application height. At the 0.6- and 0.9-m treatment heights, hand removal resulted in greatest pod counts (Table 3). At the 0.3-m height, the P-value of 0.2 indicated no differences between treatments, though the hand-rogued plot yielded higher on average than the mechanically or electrically treated plots. The greatest total sweetpotato yield was achieved by hand removing Palmer amaranth prior to reaching 0.9 m in height. Though hand removal often resulted in the greatest peanut pod count and total sweetpotato yield, the Weedpuller and Weed Zapper resulted in similar yields as hand roguing, depending on the treatment timing. With additional research to provide insight into the optimal applications, there is potential for the Weed Zapper and the Weedpuller to be used as alternatives to hand removal in peanut and sweetpotato. These results are contrary to those reported by Simard et al. (Reference Simard, Page and Nurse2019), who observed suboptimal control from using the Weedpuller in soybean. The difference in results is likely due to the taller crop height of soybean compared to peanut and sweetpotato.
Table 3. Influence of treatment method and application height on yield of ‘Walton’ peanut and ‘Covington’ sweetpotato. a, b
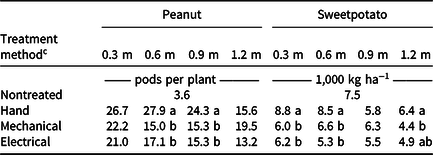
a Data are pooled across years.
b Means within a column for dependent variables followed by the same letter are not significantly different according to Tukey–Kramer honestly significant difference (α = 0.05). Means within a column not followed by a letter are not significantly different according to a nonsignificant F statistic (P > 0.05).
c Treatments were applied using the Weed Zapper Annihilator 6R30 for electrical control and the Bourquin Organic Weedpuller/roguing machine–Posi Pull for mechanical control.
Visible injury could not be consistently rated in all crops because of Palmer amaranth interference, although in sweetpotato, up to 20% injury was observed in certain plots after treatment using the Weed Zapper, depending on the environmental conditions and treatment timing (data not shown). More research is needed to assess the negative impacts that electrical treatment can have on sweetpotato. Observed injury was often located near treated Palmer amaranth. It is likely that electricity traveled through the sweetpotato that was close to or contacting the weed at the timing of treatment.
Seed Production and Viability
The nonelectrically treated control produced 11,000 seeds plant−1 4 WAI, which is less than the typical 200,000 to 600,000, because plant densities were high (approximately 50 plants m−2). Treatments at varying reproductive maturities did not reduce the seed production immediately after treatment at a 95% confidence level (Table 4). However, after treatment, plants primarily died and ceased maturation, reducing seed production at 4 WAI by 93% and 70% when treated 0 and 2 WAI, respectively. Similarly, Schreier et al. (Reference Schreier, Bish and Bradley2022) reported weed seed viability reductions from 54% to 80%. Treatments did not have a negative effect on germination or seedling length, indicating that the quality of seeds was unchanged by electrical treatment in the present study based on the variables that were recorded.
Table 4. Influence of electrical treatment on Palmer amaranth progeny seed production, germination, and seedling length. a, b

a Means followed by an asterisk are statistically different from the respective nonelectrically treated check according to Dunnett’s test (α = 0.05).
b Abbreviation: WAI, wk after first visible inflorescence.
c At the last treatment timing (4 WAI), plants in the nonelectrically treated check were large and at reproductive maturity; thus plots previously treated and the check were harvested before the last treatments were applied, to avoid seed shatter. After the 4 WAI treatment, the nonelectrically treated check was harvested again for comparison.
Economic Discussion
Each of these studies was conducted at a research station with historically high (50 to 100 plants m−2) Palmer amaranth densities. Thus these studies were conducted under weed pressures that were expected to be worse than what is found on the average North Carolina farm (K. M. Jennings, personal communication, 2021). These numbers will be used for a rough comparison of economics with the caveat that actual data will vary depending on weed densities and costs specific to individual circumstances. On average, to hand remove the weed densities in each study required 40, 81, 53, and 53 h ha−1 for removal at the 0.3-, 0.6-, 0.9-, and 1.2-m application timings, respectively. The adverse effect wage rate for employing H-2A employees in North Carolina is US$13.15 h−1 (USDOL-ETA 2021); however, this does not include additional costs of transportation, meals, housing, and fees. Using US$13.15 h−1 would equate to US$530, US$1,060, US$690, and US$690 ha−1 for removal at the 0.3-, 0.6-, 0.9-, and 1.2-m application timings, respectively, in the present study. Comparatively, a four-row (4.3-m-wide) electrical or mechanical weed control implement could cover approximately 2 ha h−1 at 4.8 km h−1, not factoring in the time required to turn around at the ends of rows and to travel between fields. Assuming the same wage rate, the cost of labor to operate the implements would be approximately US$26.30 ha−1. This leaves an approximate US$500 ha−1 difference in labor from the cheapest recorded hand-removal cost to cover the cost of equipment, fuel, and maintenance.
The cost of hand weed removal is directly related to the density of weeds present. In the present study, weed densities were much greater than would be expected in a grower field. In a survey of sweetpotato growers in North Carolina in 2018, the cost of hand weed removal was US$62 to US$370 ha−1, with a mean of US$150 ha−1 (Smith and Moore, unpublished data). The survey included primarily conventional cropping systems, though a few organic sweetpotato systems were included in the surveyed group. Using this more relevant number of US$150 ha−1 would leave a difference of approximately US$120 ha−1 between the labor cost for hand removal and electrical or mechanical control to cover the operation cost of the control implements. In 2019, the estimated cost of operation of a 190 PTO horsepower tractor was US$116 h−1 (Lattz and Schnitkey Reference Lattz and Schnitkey2019). The cost of operation will depend on power demand of the implement being used, which will be greater when using the Weed Zapper than when using the Weedpuller. However, this estimated figure will be used for discussion for both implements. At 4.8 km h−1, the cost of operating the tractor with a 4.3-m-wide implement would be US$58 ha−1. This would leave approximately US$62 ha−1 to cover the cost of the equipment and maintenance.
The cost of electric and mechanical weed control implements will vary depending on the source, model, and year. The cost of the 4.3-m electrical weed control implement is approximately US$56,000, and the cost for a Weedpuller of the same size is approximately US$14,000. With these figures in mind, one would require 903 and 226 ha treated with the electrical and mechanical implement, respectively, rather than with hand removal to pay for the cost of the implement. However, we acknowledge that the cost of hand labor would likely be higher than what was used for this discussion owing to additional costs and the cost of equipment maintenance not being included. Thus this discussion should be used for informational purposes only, and the numbers should be adjusted to fit individual circumstances. The cost of herbicides may be lower than the cost of controlling weeds with the electrical or mechanical implements and, if used as preemergence control, would offer greater yields, as there would be less total competition with the crop. However, the electrical and mechanical implements can be useful for cropping systems that are grown for markets that require the absence of synthetic herbicides or where herbicide resistance causes escapes.
Acknowledgments
The authors thank Southern Sustainable Agriculture Research and Education, the North Carolina Agricultural Foundation, the North Carolina Department of Agriculture and Consumer Services, the North Carolina College of Agriculture and Life Sciences at North Carolina State University, and the North Carolina SweetPotato Commission for funding these studies and Jim Jones for providing sweetpotato slips. The authors also thank Kira Sims, Cole Smith, Chitra, and the staff at the NCDA&CS Horticultural Crops Research Station at Clinton, NC, for aiding in managing this experiment. The authors declare no conflicts of interest.