Introduction
In today's competitive industrial world, the supply of high-purity raw materials and the production of high-quality products are of great importance. Kaolin is an industrial clay material composed primarily of kaolinite, a hydrated aluminium silicate with the chemical composition of Al2Si2O5(OH)4. Kaolin has various industrial applications, including in refractories, ceramics, pottery, fibreglass, paper filling and coating, paint and rubber, among others (Murray, Reference Murray2002). Iron oxides/oxyhydroxides and sulfides, mainly hematite, goethite, magnetite, limonite, ilmenite and pyrite, are the main impurities in kaolins, adversely affecting their quality and colour (Chandrasekhar & Ramaswamy, Reference Chandrasekhar and Ramaswamy2006; Bertolino et al., Reference Bertolino, Rossi, Scorzelli and Torem2010). Fe-minerals should be removed from kaolin to achieve acceptable quality. The methods for the removal of Fe-minerals can be classified into physical and chemical approaches, with the combination of the two methods usually being more effective. Several separation techniques including high-gradient magnetic separation (HGMS; Shoumkov et al., Reference Shoumkov, Dimitrov and Brakalov1987; Maurya & Dixit, Reference Maurya and Dixit1990; Raghavan et al., Reference Raghavan, Chandrasekhar and Damodaran1997; Chandrasekhar & Ramaswamy, Reference Chandrasekhar and Ramaswamy2002), selective flocculation (Larroyd et al., Reference Larroyd, Petter and Sampaio2002), sieving and hydrocycloning (Barrachina et al., Reference Barrachina, Calvet, Fraga and Carda2017) and flotation (Luz et al., Reference Luz, Yildirim and Yoon2000; Murray, Reference Murray2002), have been used to remove Fe-minerals from clays. Physical separation methods are mostly used for relatively coarse and liberated particles of minerals such as magnetite, hematite and pyrite. However, removing colloidal particles and hydroxide or hydrated oxide iron-bearing minerals requires the use of chemical treatment. Chemical beneficiation methods make use of leaching, usually under acidic or reducing conditions (Veglio & Toro, Reference Veglio and Toro1994; de Mesquita et al., Reference de Mesquita, Rodrigues and Gomes1996; Ambikadevi & Lalithambika, Reference Ambikadevi and Lalithambika2000; Atkinson & Fleming, Reference Atkinson and Fleming2001). Therefore, numerous leaching agents such as organic acids (de Mesquita et al., Reference de Mesquita, Rodrigues and Gomes1996; Veglio et al., Reference Veglio, Passariello, Toro and Marabini1996; Ambikadevi & Lalithambika, Reference Ambikadevi and Lalithambika2000; Tuncuk et al., Reference Tuncuk, Ciftlik, Gunes, Handiri, Ciftci and Akcıl2010; He et al., Reference He, Huang and Chen2011), sulfuric acid (H2SO4; Veglio, Reference Veglio1997; Tuncuk et al., Reference Tuncuk, Ciftlik and Akcil2013), sodium dithionite (Na2S2O4; Mehra & Jackson, Reference Mehra and Jackson1958; Thurlow, Reference Thurlow2001; Gougazeh, Reference Gougazeh2018), sodium thiosulfate (Na2S2O3; Olvera-Venegas et al., Reference Olvera-Venegas, Cruz and Lapidus2017), thiourea (H2NCSNH2), dioxide thiourea ((NH2)2CSO2; Veglio, Reference Veglio1997; Xia et al., Reference Xia, Lu, Su and Zhao2012; Lu et al., Reference Lu, Xia and Cao2017a, Reference Lu, Xia and Zhang2017b), chlorine water (Carpmael, Reference Carpmael1928; González & Ruiz, Reference González and Ruiz2006) and EDTA (Borgaard, Reference Borggaard1979), as well as thermochemical techniques (Khalifa et al., Reference Khalifa, Hajji and Ezzaouia2013, Reference Khalifa, Hajji and Ezzaouia2019), have been used to remove iron and other impurities from quartz and clay minerals. The bioleaching technique (Kostka et al., Reference Kostka, Haefele, Viehweger and Stucki1999; Lee et al., Reference Lee, Cho and Ryu2002; Cameselle et al., Reference Cameselle, Ricart, Nunez and Lema2003; Hosseini et al., Reference Hosseini, Pazouki, Ranjbar and Habibian2007; Guo et al., Reference Guo, Lin, Xu and Chen2010; He et al., Reference He, Huang and Chen2011; Zegeye et al., Reference Zegeye, Yahaya, Fialips, White, Gray and Manning2013) is also of great interest for iron removal from clay minerals. Due to their lower acidic strength than mineral acids, organic acids are more selective for Fe leaching; in addition, the texture of the kaolin is less affected when using organic acids. Furthermore, recovering the acids and neutralizing the final products are more difficult to achieve with mineral acids than organic acids, due to the greater acidic strength of the former.
Among the organic acids used as effective solvent reagents, oxalic acid (C2H2O4) has been the most promising (Panias et al., Reference Panias, Taxiarchou, Douni, Paspaliaris and Kontopoulos1996a; Calderon et al., Reference Calderon, Guillermo and Rodriguez2005; Lee et al., Reference Lee, Tran, Park, Kim and Kim2006, Reference Lee, Tran, Jung, Kim and Kim2007; Martínez-Luévanos et al., Reference Martínez-Luévanos, Rodríguez-Delgado, Uribe-Salas, Carrillo-Pedroza and Osuna-Alarcón2011; Hernandez et al., Reference Hernandez, Garcia, Cruz and Luevanos2013; Baba et al., Reference Baba, Mosobalaje, Ibrahim, Girigisu, Eletta, Aluko and Adekola2015; Taran & Aghaie, Reference Taran and Aghaie2015) because of its high reducing power, complexing capacity and acid strength (Panias et al., Reference Panias, Taxiarchou, Douni, Paspaliaris and Kontopoulos1996a; Nwoye et al., Reference Nwoye, Nwobodo, Nlebedim, Nwoye, Umana and Obasi2009; Tuncuk et al., Reference Tuncuk, Ciftlik, Gunes, Handiri, Ciftci and Akcıl2010; Barrachina et al., Reference Barrachina, Calvet, Fraga and Carda2017). Moreover, when using oxalic acid, the dissolved iron can precipitate as ferrous oxalate from the leaching solution and can be further reprocessed to recover the oxalic acid (Taxiarchou et al., Reference Taxiarchou, Panias, Douni, Paspaliaris and Kontopoulos1997; Yu et al., Reference Yu, Shi, Chen, Niu, Wang and Wan2012; Liu et al., Reference Liu, Peng, Wilson and Lundstrom2019; Schapiro et al., Reference Schapiro, Boiko and Shapiro2020).
Oxalic acid ionizes, forming bi-oxalate and oxalate ions according to the reactions in Equations 1 & 2 (Hernandez et al., Reference Hernandez, Garcia, Cruz and Luevanos2013; Schapiro et al., Reference Schapiro, Boiko and Shapiro2020):


where Kα1 and Kα2 denote the dissociation constants for the first and the second ionizable hydrogen atoms in the acid. Having an oxygen atom with a free electron pair, oxalic acid can react with both Fe3+ and Fe2+ ions in iron oxide and form ferric and ferrous oxalate complexes, as in Equations 3–6 (Panias et al., Reference Panias, Taxiarchou, Paspaliaris and Kontopoulos1996b; Lee et al., Reference Lee, Tran, Park, Kim and Kim2006, Reference Lee, Tran, Jung, Kim and Kim2007; Hernandez et al., Reference Hernandez, Garcia, Cruz and Luevanos2013; Tuncuk et al., Reference Tuncuk, Ciftlik and Akcil2013):




Ferric ion (Fe3+) is soluble only in acidic conditions (pH < 3), but ferrous ion (Fe2+) is soluble across a wide range of pH values in aqueous media. However, at alkaline and neutral pH values, Fe2+ is stable only under reducing conditions, and in the presence of oxygen or oxidation conditions it oxidizes rapidly and precipitates, yielding ferric hydroxides (Schwertmann & Taylor, Reference Schwertmann and Taylor1989). At pH 1–2, both ferrous and ferric oxalate complexes are stable; however, at pH < 1, only the ferric oxalate complex is stable. Ferric oxalate might transform into oxalate over time or in the presence of a reducing agent such as iron or ultraviolet radiation according to Equations 7–10 (Lee et al., Reference Lee, Tran, Jung, Kim and Kim2007; Yu et al., Reference Yu, Shi, Chen, Niu, Wang and Wan2012; Tuncuk et al., Reference Tuncuk, Ciftlik and Akcil2013):




where hν denotes ultraviolet radiation. The dissolution process is affected mainly by the pH of the initial solution and temperature (Panias et al., Reference Panias, Taxiarchou, Paspaliaris and Kontopoulos1996b).
In this study, a kaolin obtained from the Esteghlal Fire Clay Mine at Abadeh, southern Iran, was treated chemically with oxalic acid to remove iron-bearing minerals. However, the reagent consumption and the leaching time and temperature were not cost-effective and were unfavourable technically. Applying the HGMS technique was not possible practically due to the slime coating of iron oxide particles on the fine-grained clay minerals. To find an effective physical pretreatment method to reduce the amounts of the most leaching-resistant iron oxides before chemical treatment, an innovative pretreatment technique was applied using a pre-agitating process followed by washing the material on a 600 μm sieve to discard a significant portion of the liberated hematite particles. In this manner, the leaching time and consumption of oxalic acid during leaching decreased significantly.
Materials and methods
Materials and characterization
A raw kaolin sample was obtained from the Esteghlal Fire Clay Mine, Abadeh, southern Iran. The mineralogical composition of the sample was determined using X-ray powder diffraction (XRD). Quartz and clay minerals, mainly kaolinite and lesser amounts of pyrophyllite and muscovite, were the main constituents (Fig. 1). Hematite was identified as the only iron-bearing mineral in the sample. Other iron oxides/oxyhydroxides were not detected, possibly due to their trace abundances.

Figure 1. XRD trace of the raw kaolin sample.
The chemical composition of the sample was assessed using X-ray fluorescence (XRF) spectrometry (Table 1). The approximate amount of iron oxides (Fe2O3) in the sample was 13.75 wt.%, corresponding to 9.63 wt.% Fe. In addition, the Fe contents of the samples and products were determined using the potassium dichromate titration method. Based on the titration analysis, the iron content of the sample was 9.76 wt.%, corresponding to 13.94 wt.% Fe2O3, which is in good agreement with the XRF results. The Al2O3 and SiO2 contents were 24.64 and 52.55 wt.%, respectively, the TiO2 content was 1.42 wt.% and the total alkaline oxide (Na2O and K2O) and alkaline earth oxide (MgO and CaO) contents were 3.19 and 1.98 wt.%, respectively. All chemicals used were of analytical grade.
Table 1. Chemical composition of the raw material.

LOI = loss on ignition.
Physical pretreatment method
A certain amount of the kaolin was crushed using a jaw crusher or ground within a ceramic ball mill and was then agitated in a mixing tank at an agitating speed of 2000 rpm for a given time. This was then washed on a series of laboratory sieves using a nozzle spray with a low flow of pressurized water.
Leaching procedure
The leaching tests were carried out in a three-port glass reactor (1 L). The slurry was prepared by mixing dry kaolin with tap water in a stirring reactor at a given mass ratio. After appropriate mixing, a certain amount of oxalic acid was added, and the leaching experiments were conducted under controlled stirring and temperature conditions for a given time under reflux conditions. Subsequently, the slurry was filtered, washed and dried at 90°C. These experiments were conducted both on the raw kaolin and on the pretreated kaolin.
Results and discussion
Physical characterization and separation
To investigate the amount and type of interlocking of iron oxide particles within clay minerals, polished sections of various size fractions were prepared and studied using polarized reflected light microscopy (Fig. 2). Hematite and goethite were the main iron phases detected, often forming massive lumps or veins within clay minerals. There was not much complex interlocking of iron oxide grains within the clay minerals. As clay minerals have a softer texture than iron oxides, their separation by comminution and washing seemed possible. In addition, iron oxide particles are less abundant in finer fractions, as was confirmed using XRD (see below). The liberation degree of the particles was also calculated semi-quantitatively using optical image analysis by counting the liberated and locked particles (Table 2).

Figure 2. Micrographs of polished cross-sections of the various size fractions. G = goethite; H = hematite.
Table 2. Degree of liberation of iron oxide particles.

To investigate the size distribution, three similar representative samples of crushed particles were examined using a set of laboratory-standard sieves of the ASTM series under three conditions (dry, wet and pre-agitated) in a mixing tank followed by high-pressure washing on sieves. The particle-size distribution curves of the samples prepared under various conditions show considerable differences (Fig. 3). Dry sieving analysis showed a pseudo-granular distribution in which the clay particles were not separated from each other completely, and the particle-size distribution curve was shifted towards coarser particles, indicating the aggregation of clay particles. The particle-size distribution curves of the wet and pretreated samples analysed were shifted towards finer particles. The d 80 values of the dry, wet and pretreated samples were ~3000, 1500 and 900 μm, respectively.
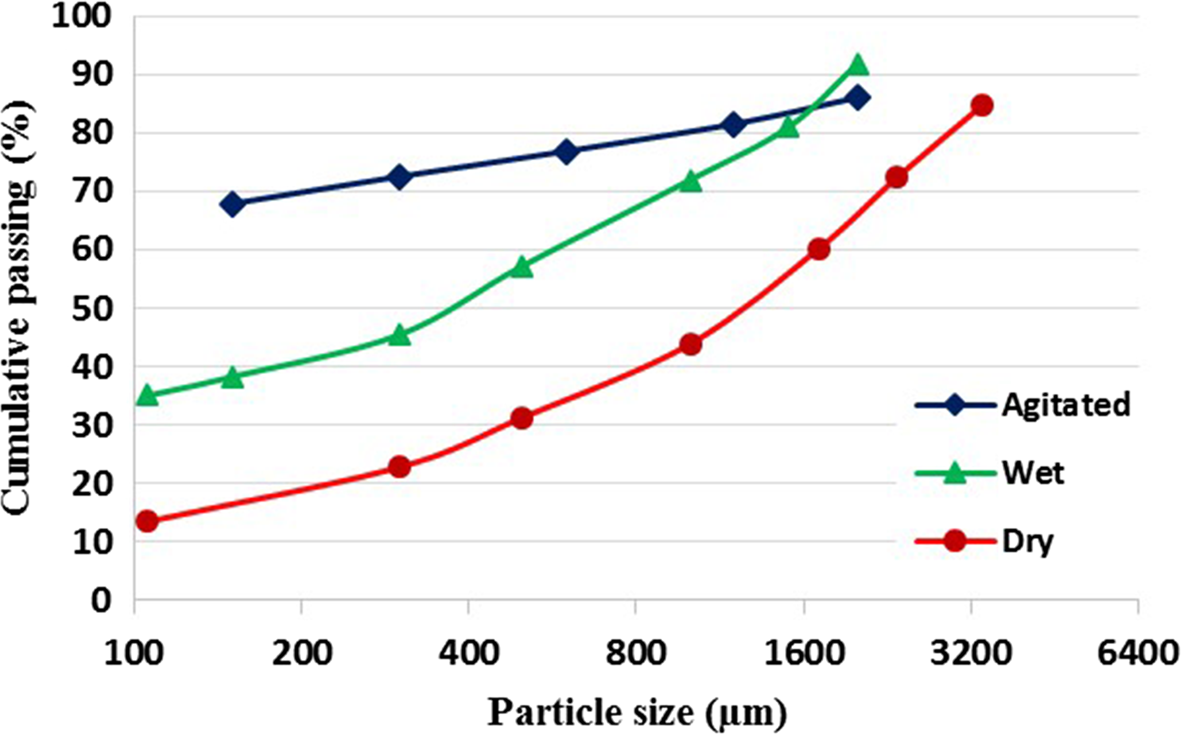
Figure 3. Particle-size distribution curves of crushed samples classified under dry, wet and pre-agitated conditions.
To investigate the distribution of iron in the various size fractions further, 500 g of crushed samples were classified into six fractions (Table 3) after applying the pretreatment procedure. The results indicated that greater iron contents were related to coarser particles. Hence, the >2000 μm fraction, containing 26.34 wt.% Fe, was equivalent to 14% of the total mass, which accounted for 37.91 wt.% of the total iron content in the sample. In other words, if the >2000 μm fraction was discarded, 37.91 wt.% of the iron would be removed, and the iron content of the remaining sample would reduce to 7.06 wt.%. As another example, total fractions >600 μm, corresponding to 23.17 wt.% of the total mass, had a cumulative iron content of 22.46 wt.%. Thus, by removing these fractions from the samples, 53.49 wt.% of total iron would be removed and the iron content of the remaining fractions would decrease to 5.93 wt.%.
Table 3. Iron content (wt.%) in various size fractions after crushing followed by pretreatment.

The XRD traces of the three fractions (>2000, 300–600 and <100 μm) are shown in Fig. 4. The samples consist of clay minerals, quartz and hematite. The abundance of hematite, as the most significant iron impurity, was greater in coarse fractions and decreased with decreasing particle size.
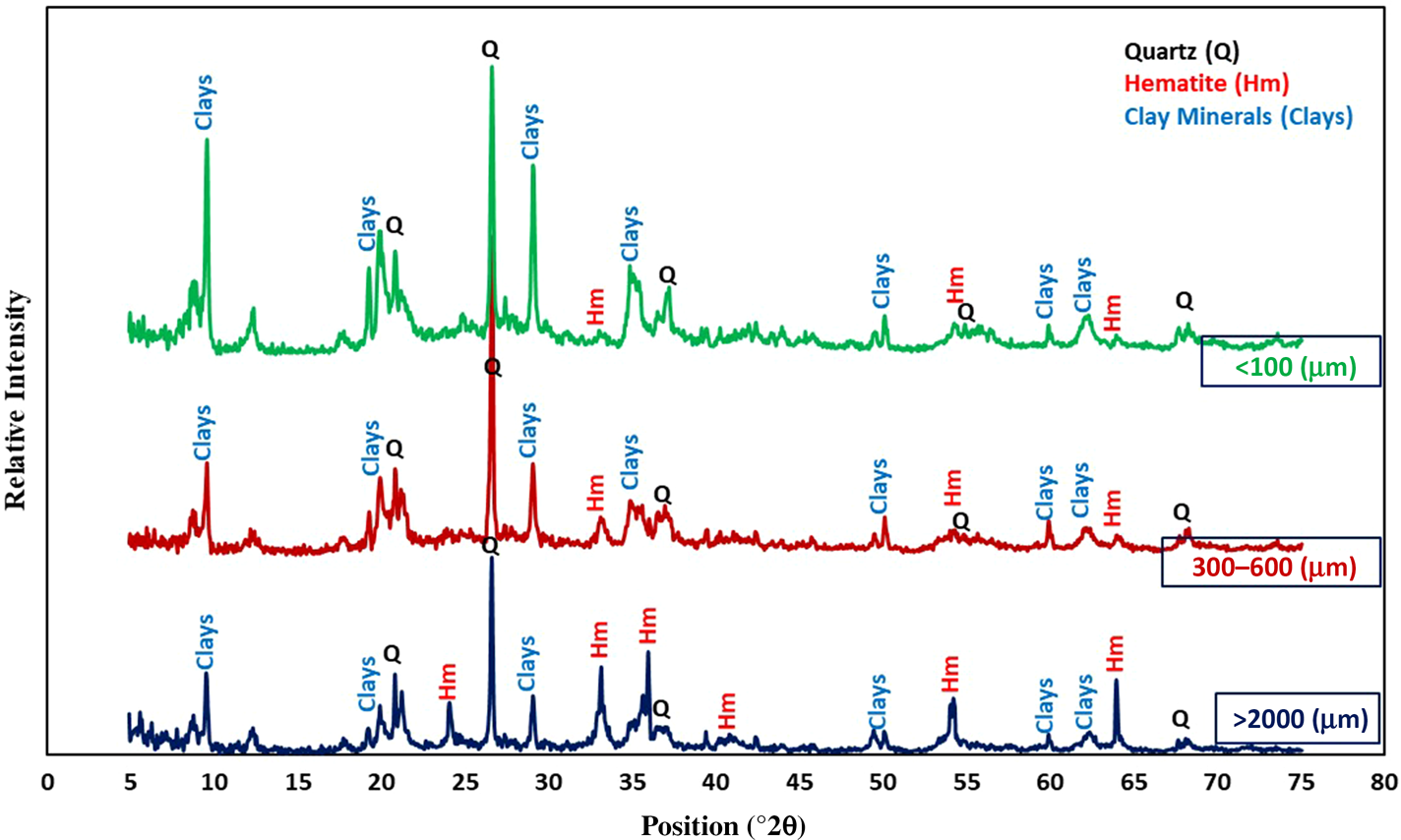
Figure 4. XRD traces of >2000, 300–600 and <100 μm size fractions.
Colour change can be observed in the aforementioned size fractions in Fig. 5. For better comparison of the colour change, powdered samples are also shown in Fig. 5. A darker colour indicates a greater abundance of iron and a lighter colour indicates a lesser amount of iron in the sample, suggesting the greater grindability of clay minerals compared to hematite.

Figure 5. Images of coarse particles and powders of >2000, 300–600 and <100 μm size fractions.
To investigate the effect of wet grinding and high-pressure washing on the separation of iron oxides from clay minerals at smaller particle sizes, similar samples were ground wet using a ceramic ball mill for various grinding times (5, 8, 10 and 15 min), and the relevant size distribution curves are presented in Fig. 6. The wet-ground samples were agitated in a mixing tank at a stirring rate of 2000 rpm for 10 min and passed through a set of ASTM sieves under pressurized water flow. Grinding the samples for 10 min followed by agitation and washing on sieves resulted in a d 80 value of ~600 μm. Accordingly, the particles achieved a sufficient degree of liberation to meet the requirements of the leaching process.
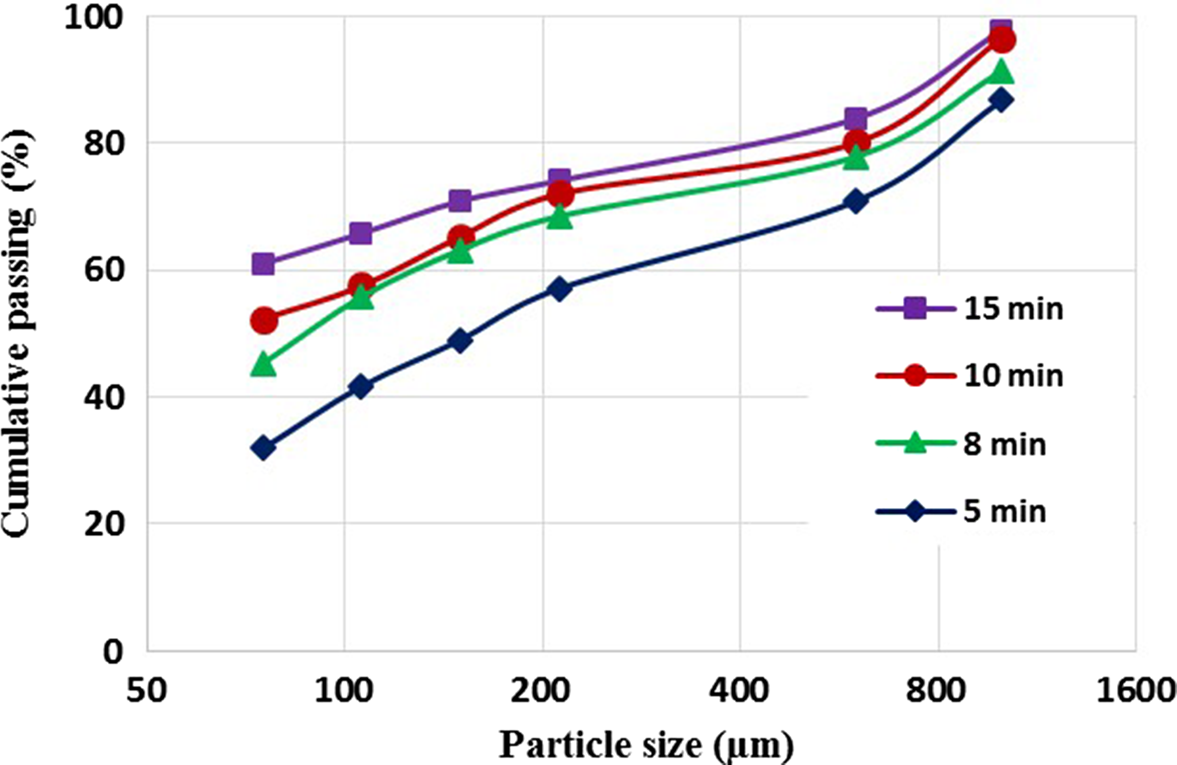
Figure 6. Particle-size distribution curves of wet-ground pre-agitated samples after various reaction times.
The distributions of iron in the various size fractions of a wet-ground sample after 10 min followed by pretreatment are listed in Table 4. Some 19.90 wt.% of the total sample was in the >600 μm fraction; by discarding this fraction, ~54.30 wt.% of the iron content of the sample was removed, and the iron content in the passing fractions was reduced to 5.57 wt.%.
Table 4. Distribution of iron content (wt.%) in various size fractions after grinding.

In all of the comminution and classification procedures mentioned above, removing the >600 μm fractions removed part of the iron content of the sample and reduced the iron content in the passing fractions. During this separation process, some of the clay was, inevitably, discarded. Therefore, the most favourable conditions for separation in this process involved the achievement of the lowest iron contents in remaining fractions and the greatest iron removal and lowest removal of clay minerals in the discarded fractions. It was impossible to achieve all of these favourable conditions using such a separation method, but conditions close to such favourable conditions could be selected. Grinding the sample for 10 min and washing the pre-agitated sample on a 600 μm sieve constituted the most promising procedure as a pretreatment method.
Leaching tests
Leaching tests were conducted to reduce the iron content of kaolin to <1 wt.%, which would enable the kaolin to be used in relevant industries. These tests were performed both on raw kaolin samples with an iron content of 9.76 wt.% and on the samples with an iron content of 5.65 wt.% pretreated with 10 min of wet grinding followed by agitation at 2000 rpm and high-pressure washing on a 600 μm sieve. Both the crushed and ground samples, whose coarse fraction (i.e. >600 μm) had been discarded, were appropriate for the leaching process in terms of their iron content (Tables 3 & 4); however, the wet-ground and pretreated sample passing 600 μm was preferred over the crushed sample due to ease of agitation and the reduced amount of clay loss.
Leaching behaviour of raw kaolin
The effects of oxalic acid concentration and leaching time on the dissolution of iron as a function of temperature are given in Fig. 7. The dissolution rate of iron increased from 25 to 97°C. The effect of acid concentration was more significant for the dissolution of iron than leaching time. Thus, for an acid concentration of 0.5 M, iron removal exceeded 90% at all leaching times. However, the leaching efficiency of raw kaolin was not favourable at <2 h (results not shown).
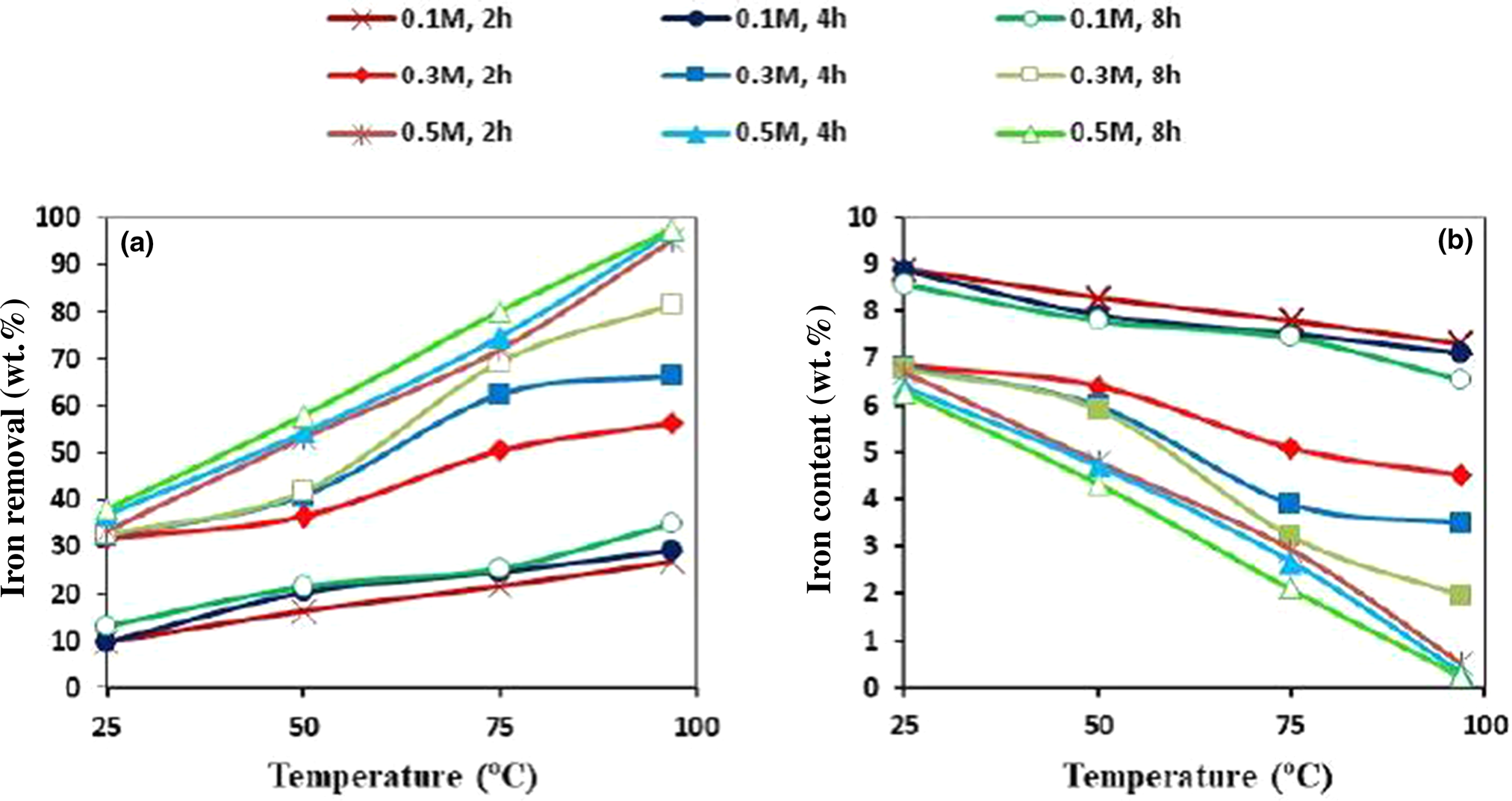
Figure 7. (a) Iron removal (wt.%) and (b) iron content (wt.%) as a function of leaching temperature under various acid concentration and leaching time conditions.
The best conditions for raw material leaching were found to be 97°C and 0.5 M oxalic acid concentration for 2 h, and the final product was of good quality in terms of iron content and whiteness but was not cost-effective.
Leaching of pretreated kaolin
Due to the iron dissolution rate, acid consumption and corrosion problems that might result in high operating costs, direct leaching of the raw material without pretreatment was not cost-effective. Therefore, the pretreated material was used for the remaining leaching tests and for optimization of the effective parameters. To shed light on the effect of leaching temperature on iron dissolution, leaching tests were performed in the range of 50–100°C using 0.5 M oxalic acid for 120 min. Only at the boiling point of the slurry would the removal of iron from kaolin be effective, and therefore a temperature of 97°C was adopted in all subsequent tests.
Oxalic acid concentration had a significant effect on iron leaching from kaolin. The effect of oxalic acid concentration on the dissolution of iron at 97°C was investigated for the concentration range of 0.1–0.3 M. Increased iron removal and decreased iron content of the residue were observed with increasing oxalic acid concentration (Fig. 8). Iron removal reached 92%, yielding an iron content of 0.5 wt.% in the residue. Therefore, the minimum oxalic acid concentration needed to achieve the desired iron content in kaolin was 0.3 M.
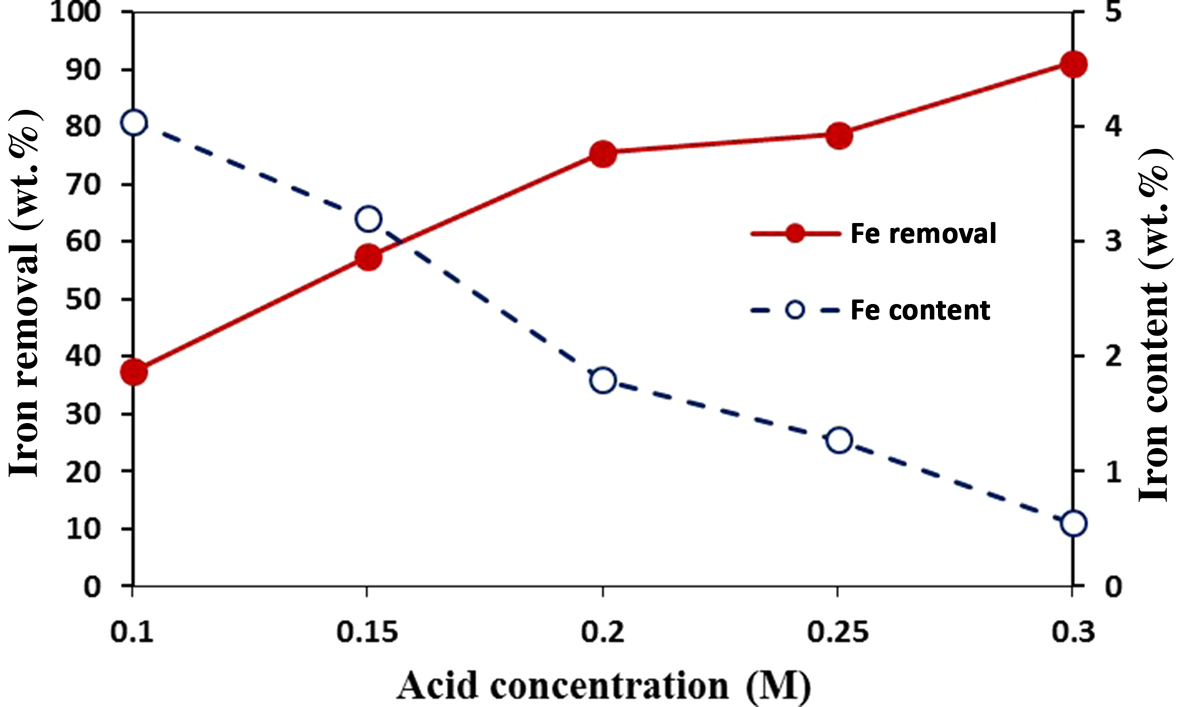
Figure 8. Iron removal and iron content (wt.%) at 97°C with oxalic acid of various concentrations for a reaction time of 120 min.
All of the previous leaching experiments were carried out for particle sizes <100 μm in which a complete degree of liberation of iron-bearing mineral particles from clays was achieved. However, in the leaching process a complete degree of liberation is not necessary; a degree of liberation that causes the leaching agent to come into contact with the target particle would be sufficient. However, excessive comminution, in addition to excessive energy consumption, leads to problems in filtration. Accordingly, leaching experiments were carried out with particle sizes of <600, <300 and <100 μm, and the results are shown in Fig. 9.

Figure 9. Effect of particle size on iron removal and iron content (wt.%; temperature = 97°C, stirring speed = 1200 rpm, leaching time = 120 min, oxalic acid concentration = 0.3 M, L/S ratio = 10).
With increasing particle size, the degree of iron dissolution decreased; however, the iron contents of the final products were <1 wt.% for all particle sizes. As a result, for particle sizes <600 μm, the desired efficiency of leaching was achieved. Particle sizes >600 μm were not available due to the pretreatment process. Therefore, the maximum size of the particles for achieving optimal leaching conditions was 600 μm, and the following experiments were carried out within the particle size range of <600 μm.
The effect of the liquid-to-solid (L/S) ratio on iron dissolution was examined at 97°C at a stirring speed of 1200 rpm, a leaching time of 120 min and an oxalic acid concentration 0.3 M. The percentages of iron removal and final iron contents for the L/S ratios of 1, 2, 4, 6, 8 and 10 are presented in Fig. 10. For L/S ratios >2, the desired dissolution of iron and thus the desired iron contents of the final product were obtained.

Figure 10. Effect of liquid-to-solid ratio on iron dissolution from kaolin (temperature = 97°C, stirring speed = 1200 rpm, leaching time = 120 min, oxalic acid concentration = 0.3 M).
Due to water-shortage issues, a low L/S ratio is desirable; however, stirring the slurry in very low L/S ratios also causes problems. Taking into account both of these difficulties, the optimum value of the L/S ratio was set to 4. For further investigation, the effect of the stirring speed of the slurry at L/S ratios of 2, 4 and 10 at 97°C, a leaching time of 120 min and an oxalic acid concentration 0.3 M was studied. At low stirring speeds (i.e. 300 and 500 rpm), the effect of the L/S ratio was clear; as the L/S ratio decreased, the final iron content increased. However, at high stirring speeds (i.e. >800 rpm), the L/S ratio did not affect leaching significantly (Fig. 11). For all of the stirring speeds and all of the L/S ratios, the iron contents were <1 wt.%, indicating that changes in the stirring speed did not have a significant effect on the leaching process. Therefore, a stirring speed of 800 rpm would be sufficient to mix the pulp properly, and this relatively low stirring speed provides significant economic and technical advantages.

Figure 11. Effect of stirring speed on iron dissolution from kaolin at L/S ratios of 2, 4 and 10 (temperature = 97°C, leaching time = 120 min, oxalic acid concentration = 0.3 M).
Based on previous experiments, the maximum time required for leaching of the pretreated sample was 120 min. After optimizing all of the other parameters (i.e. 97°C, 800 rpm stirring speed, 0.3 M oxalic acid and L/S ratio of 4), further investigations were conducted to optimize the leaching time. Reaction times of 30, 60, 90 and 120 min under the aforementioned conditions were investigated, and the results are presented in Fig. 12. With increasing leaching time, the efficiency of the leaching increased; leaching conditions were achieved after 60 min. Therefore, the minimum time required to achieve the desired result was 60 min.
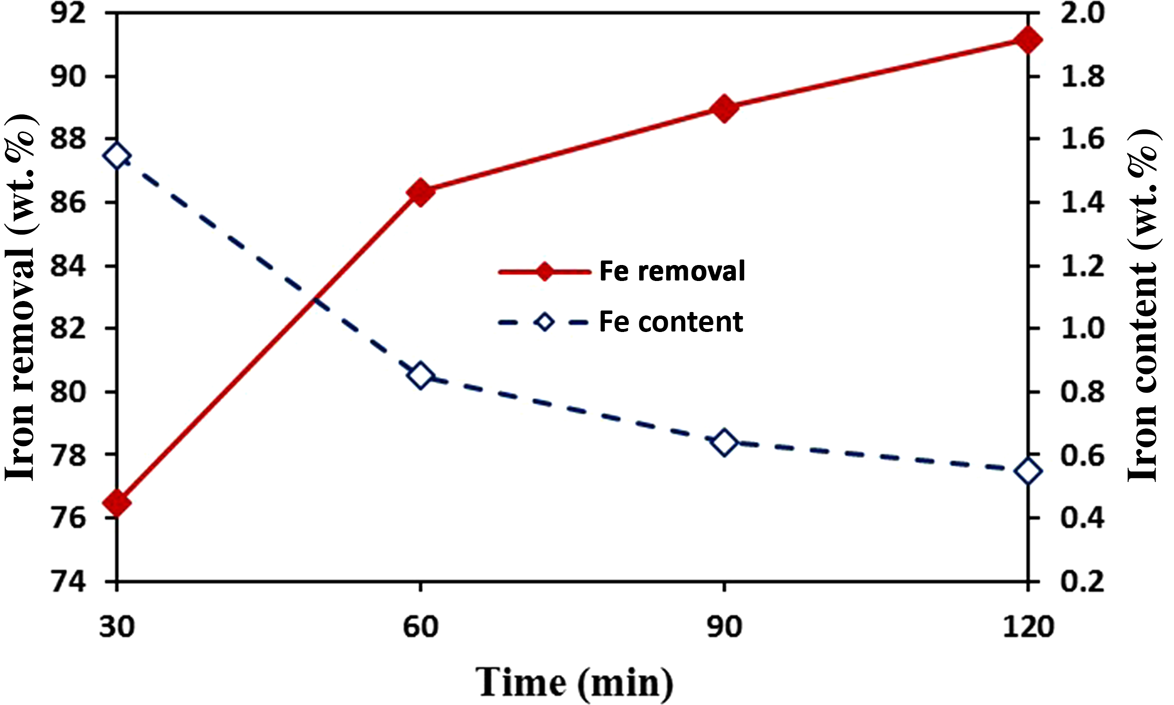
Figure 12. Effect of leaching time on iron dissolution from kaolin (temperature = 97°C, L/S ratio = 4, oxalic acid concentration = 0.3 M, stirring speed = 800 rpm).
The procedure applied in this work allowed for significant improvement in the colour of the final product to be obtained. The changes in the colour of pulp and leaching solution before and after the leaching process are shown in Fig. 13. The white kaolin sediment at the end of the leaching process under optimum conditions (i.e. 97°C for 60 min with an L/S ratio of 4, oxalic acid concentration of 0.3 M and stirring speed of 800 rpm) demonstrated successful removal of iron, leading to an increase in the quality of the product. The green supernatant solution indicated that the extracted iron from the kaolin was in the form of iron oxalate complexes.

Figure 13. Changes to slurry colour before and after leaching (left to right: before leaching, after leaching and separated solid–liquid, respectively).
Overall, if raw kaolin is pretreated with the innovative physical separation process used in this study by removing a maximum of 20% of the raw material, the iron content of the remaining clay (<600 μm in size) would not exceed 6 wt.%. Therefore, under optimum leaching conditions (i.e. temperature of 97°C, oxalic acid concentration of 0.3 M, L/S ratio of 4, particle size of <600 μm, leaching time of 60 min and a stirring speed of the pulp of 800 rpm), iron would be removed from kaolin successfully and the iron content would not exceed 1 wt.%.
Summary and conclusions
Iron removal from a kaolin sample with 9.76 wt.% Fe, mainly in the form of hematite, by oxalic acid using an innovative physical pretreatment method was studied.
Initial physical characterization regarding the degree of liberation indicated that hematite, as the main iron oxide impurity, was often in the form of massive lumps or veins within the clay minerals without complex interlocking. An effective physical separation method was applied using a pre-agitation stage followed by high-pressure washing to remove leaching-resistant iron oxides selectively from the kaolin before the leaching process. The compact structure of fine-grained kaolin was destroyed gradually during agitation and washing, such that the hematite particles were released and became concentrated in the coarse fractions.
During the pretreatment, by washing the wet-ground and pre-agitated raw kaolin on a 600 μm sieve, a maximum of 20 wt.% of the raw material was discarded, which was equivalent to the removal of >50 wt.% of the total iron content of the sample, leading to the reduction of the iron content to <6 wt.% in the remaining part, rendering kaolin samples more appropriate for the leaching process compared to the original samples.
The oxalic acid leaching tests performed on the pretreated kaolin showed that the iron impurities of kaolin could be leached out successfully after 60 min at 97°C with an L/S ratio of 4 and a stirring speed of 800 rpm using 0.3 M oxalic acid solution under atmospheric pressure, which resulted in the reduction of the iron content to <1 wt.% in the final product.
Acknowledgements
The author thanks the Esteghlal Fire Clay Mine, Abadeh, for financial support (No. 98/19327) of this work and the University of Kashan for providing laboratory resources.
Conflicts of interest
The author declares that he has no known competing financial interests or personal relationships that could have appeared to influence the work reported in this paper.